We always have turkey for Thanksgiving. I mean who doesn’t? My job wasn’t to cook it, though; it was to eat it.
Designing a Steam System for Brewing
Craft breweries are opening at a rate of one per day, and many require a steam boiler in their brewing process. Brewery steam systems are different than space heating applications as comfort steam heating systems are designed to operate on 2 pounds of pressure while many brewers operate at pressures closer to 15 psi. The following are some often overlooked items when designing a craft brewer steam system.
Do I need a boiler room?
Since most new brewers are located in buildings which previously had no boiler, you have to consult the local codes to see if a separate boiler room is needed. According to the International Building Code, Table 508.2.5 2009, you must provide 1-hr fire separation when the boiler is over 15 psi AND 10 hp. Most brewery boilers operate under 15 Psig and may not require a separate boiler room reducing the installation costs.
Sizing the boiler
The most important part of the steam system design is to properly size the boiler. An oversized boiler can result in frequent cycling, while an undersized boiler may never be able to meet the temperature requirements of the brewery. Either circumstance will adversely affect the brewing process.
A steam boiler should be sized according to the connected load. The connected load includes all the vessels and tanks as well as the piping. The manufacturer of the brewing equipment should provide the Btu consumption of their equipment. Another sizing consideration is the planned expansion of the brewery. Since the market is growing so quickly, the boiler you design today may be undersized next year. If you do an internet search, there are many rules of thumb for sizing a brewery boiler including:
- 50,000 Btuh per barrel of capacity
- 1-2 Boiler hp (BHP) per brew barrel
- 1 BHP per barrel for smaller brewers and 2 BHP for brewers per barrel with large hot liquor tanks
As with most rules of thumb, they may not be accurate in every instance. According to brew industry design expert Blaine Clouston with Simplified Stainless, the equipment manufacturers generally ensure the equipment can meet the following:
Brewkettle heating — 1.5˚F/minute
Brewkettle, evaporation — 5- 6%/hr
Mash vessel heating — 1.5˚F/minute
Hot liquor tank — Ability to heat water one and a half times the brewhouse size in four hours. Example: A 10-barrel system would typically use up to 15 barrels in hot liquor
Based on his engineering background, Clouston has some shortcuts which will be more accurate for sizing (Bbl = Barrel):
- Brewkettle heating and boiling = 32,000 Btuh/bbl
- Hot liquor heating from 60˚-175˚F in four hours = 19,500 Btuh/bbl
- Mash vessel heating = 29,000 Btuh/bbl
Additional thoughts about sizing. Part of the sizing calculation is whether the steam consuming components will be operated separately or simultaneously as this affects the boiler and pipe sizing. Another item to consider is the energy required to heat all the pipes from a cold start. A rule of thumb is to add an additional one-third of the process load for the cold piping. Brewery elevation must also be factored into the design as well.
Pipe size. When installing a steam system, the installation of the equipment is crucial. If the piping is too large, it could inflate the installation cost. If the piping is too small, the boiler will cycle continuously affecting the ability to brew. Schedule 80 pipe is recommended for the condensate piping due to carbonic acids found in condensate. The near boiler piping on most boilers is crucial, as it is used to assure dry steam to the plant. Be sure to follow the manufacturer’s recommendations.
Steam velocity. Steam velocity is critical as excessive velocity could pull water from the boiler and create wet steam or water hammer. The pipe size could also affect the steam velocity. Verify with the boiler manufacturer the design velocity they recommend for their equipment. Some may require low velocity while others can tolerate the higher velocities.
Valve opening speed. If the system uses quick opening valves, the water could be sucked from the boiler if the valve opens too rapidly.
Vacuum. Control valves in a steam system could allow a vacuum to form. When water turns to steam, it expands at 1,600 its volume. This expansion pushes the air from the space and piping. When the steam condenses, the space that was filled with steam will fill with air. If a valve is closed and limits air from entering the space, a vacuum will form. This vacuum will create chaos inside the steam system. A vacuum breaker could alleviate the issues.
Boiler efficiency. Most steam boilers will have an efficiency range between 80% and 85%.
High-pressure or low-pressure? A low-pressure steam boiler is designed to operate at pressures below 15 Psig, and a high-pressure steam boiler operates above 15 Psig. A high-pressure boiler will allow smaller pipes and quicker heating. A low-pressure boiler will have lower operating, maintenance, and insurance costs. In addition, many municipalities require a full-time boiler operator and a separate boiler room if using a high-pressure steam boiler. This could add many thousands of dollars to the installation and operating costs. Brewing system manufacturers typically recommend a low-pressure boiler when the brewery is up to 50 barrels in capacity and a high-pressure boiler when the capacity is greater than 50.
Used vs new. I would hesitate to buy a used steam boiler since it could have internal damage or scaling that is difficult to see. This could cause excess maintenance costs, leaks, and downtime. The boiler, if it was used for space heating, was operating at pressures much lower than those required for a brewery. If considering a used boiler, verify it has been tested with a thorough internal inspection and pressure test.
Pipe insulation. An uninsulated steam pipe will allow the steam to condense. This cools the steam, reducing the efficiency and increasing the maintenance of the system. The International Mechanical Code requires pipe insulation on all projects. Consider insulating the condensate piping as this will reduce the damage from carbonic acid on the inside of the pipes.
Burner types. Steam boilers will come with either an atmospheric or power burner. The less expensive atmospheric burner has a slightly lower efficiency but a quicker start time than a power burner. When a power burner starts, there is a purge time of anywhere from 30 seconds to several minutes. During the purge, the burner blows air into the combustion chamber to void it of combustible gases before it lights. Boiler cycling can drop the steam pressure below what is needed for a rolling boil. A modulating or multistage burner will reduce the cycling.
Boiler room accessories. To properly operate the boiler, there are certain accessories required or recommended for the steam system.
Boiler feed system. A boiler feed system is a large tank that collects the condensate return and fresh makeup water for the system. The tank will have one or several pumps that feed the water to the boiler when the water level drops inside the boiler as sensed by a level control located on the boiler. The control will have two switches set at different elevations. The highest switch will energize the feed water pump or valve to replenish the water steamed away. If the water level continues to drop, the power to the burner will be interrupted stopping the heating process. This is to protect the boiler as well as the facility. The failure of the low water cutoff control is the leading mechanical cause of boiler accidents.
Condensate transfer tank. This tank is used for transferring hot condensate back to the boiler feed unit. Some of the older boiler rooms used these instead of a boiler feed unit when the boiler water level was not critical. When using a low-mass boiler, the use of a condensate transfer tank in lieu of a boiler feed system can lead to a flooded boiler and lost system water.
Blowdown tank or cooler. A steam boiler will require regular blow downs to remove undesirable items in the boiler such as solids or oils and to test the low water cutoffs. The International Plumbing Code 701.7 states the boiler blow off temperature must be below 140˚F. If you allow the hot condensate to enter the drain piping, it could warp or destroy the piping. For this reason, a blowdown tank or cooler is installed. A blowdown tank is an ASME code tank sized large enough to hold the blowdown of a boiler until it is cooled (usually enough for three blowdowns). When the tank is full, the new hot blowdown displaces the older, cooled blowdown. A blowdown cooler (or separator) is smaller than a blowdown tank and mixes city water into the boiler blow down water to reduce the temperature to 140˚F or lower.
Water treatment. Treatment is crucial for steam boilers as it will extend the life of the boiler and piping. It will also maintain the efficiency of the system. If the steam system loses water and has to make up fresh water, this new water will have solids that will adhere to the boiler heating surfaces causing scale, reducing the heat transfer ability. In addition, the fresh water will have oxygen which will pit the inside of the boiler and piping. Carbonic acid is also a concern as it is formed when carbon dioxide mixes with water, typically in the condensate piping. A water treatment professional should be consulted. Some boiler feed manufacturers will void the warranty if the treatment chemicals are fed directly to the boiler feed tank and treatment has to be injected into the condensate return piping before the tank.
According to Ryan Wohlfarth with Rite Boilers, “Water treatment is especially important in the brewing industry because of the downtime of the systems. A hot system helps remove oxygen from the water, but when the system is allowed to cool (non-brewing days) oxygen will find its way into the system and can attack the boiler and piping. Always check with your water treatment specialist if your steam will be in direct contact with any of the products being produced as it may require food grade chemicals and/or the elimination of chemicals.”
Steam cleaning. Ken Womack with Superior Boiler Works suggests that food grade water treatment chemicals or special filtration should also be used if the steam from the boiler is used for cleaning the kegs or process equipment where it comes in contact with the products.
Water meter. I like to add a water meter to the makeup water line to monitor water makeup to the system, since makeup water is a boiler killer. This could also be useful to the water treatment professional as it will help them provide the proper treatment. It is common to have a small amount of water lost during normal operation.
Water softener. A water softener is recommended for a steam boiler. The softener removes some of the hardness from the feed water reducing the chance of scale buildup on the water side of the boiler. The boiler manufacturer will advise you of the water quality they require for their boiler.
Steam pressure. One of the common issues with a brewery boiler is the setting of the steam pressure control. If the steam pressure is too low, the brewer cannot get the rolling boil they need for the process. If the pressure is too high, the relief valve can open and lose all the steam also affecting the brew process or the limit control will trip requiring a manual reset. Most brewers adjust the pressure setting between 12 to 14.5 pounds pressure. This is very close to the relief valve and limit pressure control setting.
Relief valves. Low pressure steam boilers have a relief valve setting of 15 Psig. Many relief valve manufacturers do not want the boiler operated at the setting of their relief valve. For example, the installation instructions for a Conbraco Model 12-14 relief valve states, The minimum required pressure margin for this type of valve is 4 PSI. UNDER NO CIRCUMSTANCES SHOULD THIS MARGIN BE LESS THAN 4 PSI!
This means the boiler setting should be no higher than 11 psi. If the boiler is operated at the setting of the relief valve, it may open and lose all the steam and water from the boiler. The discharge of the relief valve should include a drip pan well that will limit the weight on the relief valve and allow the drainage of any water in the discharge pipe of the relief valve.
The discharge piping should be the same diameter of the relief valve opening. I visited a job site where the installer installed a 3/4-in bushing on the 2-in outlet of the relief valve and piped the discharge piping with 3/4-in pipe. When asked why he did, he informed me he did not have any 2-in pipe but had plenty of 3/4-in. I informed him it had to be changed.
Can the boiler breathe? Combustion air is crucial to the safe operation of a boiler. The International Mechanical Code requires the following combustion air sizing:
- Two openings: one within a foot of the ceiling and one within a foot of the floor.
- Vertical opening: 1 in of free area* for each 4,000 Btuh input of the appliances.
- Horizontal opening: 1 in of free area* for each 2,000 Btuh input of the appliances.
- Mechanical: One cfm of air for each 2,400 Btuh input of the appliances.
- Indoor air: 50 cubic ft of area for each 1,000 Btuh of the appliances.
- *Free area: Typically 75% of metal louver and 50% of wooden louver.
If using motorized combustion air dampers, an interlock should be installed on the driven member of the damper to verify opening before allowing the boiler to fire.
Would you like to learn more from Ray Wohlfarth? Check out his seminars, books, and blog about brewing with steam.
Leave a comment
Related Posts
I had written a story for Plumbing & Mechanical a while back about a fella in Canada who sent me this email: "Our problem is that five out of hundreds of univentilator co...
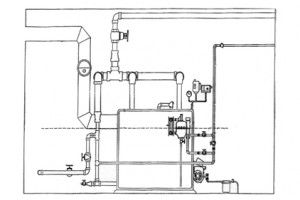
I love all the advances taking place in the world of hydronics, but I’m still seeing plenty of steam systems out there in our older cities, so knowing about dry steam wil...