We always have turkey for Thanksgiving. I mean who doesn’t? My job wasn’t to cook it, though; it was to eat it.
How Boiler Maintenance Affects Life Cycle Costs
Does Maintenance Save Money?
There are many numbers thrown about estimating the savings by performing certain maintenance activities. I remember meeting with a potential customer and showing him the list of estimated savings possible by performing various maintenance tasks. The owner looked at the list and said, If I do all these tasks, the utility company will owe me money each month because the total was in excess of 100%. Maintenance people are often jaded by the “savings” thrown about by vendors for using their services or equipment. It has taken me most of my career to realize facilities are more concerned with downtime and comfort complaints than they are with energy savings. While I acknowledge savings are possible with proper maintenance, I like to consider how maintenance, or more appropriately the lack of maintenance, can affect equipment life.
I attended a local ASHRAE meeting and the presenter from Europe discussed the philosophical differences between the maintenance departments in Europe and here in the United States. In Europe, the maintenance departments are treated as equals and with the same respect as other departments in the facility. Sadly, that is not the case here. The maintenance departments here are treated like the crazy uncle we invite to holiday dinners. The Europeans realize how the equipment maintenance directly impacts the operation and their mission statement. When the budget is tight on this side of the pond, the maintenance department is usually the first to feel the budget cuts, which could be a huge mistake. This leads to Deferred Maintenance. Deferred Maintenance is the practice of postponing maintenance activities such as repairs or preventive maintenance to save costs, meet budget funding levels, or reduce labor costs.
The error administrators make is to think the maintenance department is strictly a cost source for the facility. Rather, I believe it should be considered a cost avoidance department. Maintenance expert Rick Biedenweg of Pacific Partners Consulting Group, has performed research which suggests every dollar in deferred maintenance equals 4 dollars in capital renewal or equipment replacement costs. Management consultant, David Tod Geaslin, has a theory called Inverse Square Rule for Deferred Maintenance. His theory suggests the cost of allowing a breakdown on a piece of equipment is about 15 times the cost of a repair. Consider you are driving your vehicle and hear a high pitched squeal when you apply the brakes. This squeal is a warning meaning the brake pads are getting low. New brake pads cost about $50.00.
If you decide to ignore the problem, the brakes will eventually destroy the rotor and possibly cause an accident or a break down requiring a tow truck, making the repair costs much higher than the price of brake pads.
Deferred maintenance is becoming a critical problem as more facilities are slashing maintenance budgets. The federal government estimates a figure of $183.5 billion dollars in deferred maintenance for their buildings. Another study by the Government Accountability Office (GAO) suggests the nation’s k-12 schools have a deferred maintenance of $542 billion dollars. According to a report in the Hechinger Report, deferred maintenance has reached over $30 billion in the nation’s colleges and universities. If these figures are correct, it could mean massive amounts of money will be required if and when the equipment fails. The American Society of Civil Engineers give a grade of D for the infrastructure of the nation’s school buildings.
When you specify, design, or install a replacement piece of equipment, the owner should be encouraged to properly maintain their new equipment. A common issue with facilities is they always seem to find the funding for a replacement but rarely have money for the maintenance. This strategy could be tolerated better with the older equipment but maintenance is critical with new equipment. The newer, more efficient systems have tighter tolerances and thinner heat exchanger surfaces so regular maintenance is essential. The funny thing is a properly maintained and an un-maintained system look almost identical. As a way of combatting the problem, many designers and installers are including a long-term maintenance contract in the specifications or sales price to insure the maintenance is performed. The drawback to this is the owner is stuck with the original company and cannot choose a different vendor.
The older it gets
The maintenance required to keep the boiler operating properly increases with age. Consider a boiler installed in an area with 4,000 heating hours per season and the boiler operates roughly half those hours. If the boiler was an automobile operating at an average speed of 25 miles per hour, it would equate to 50,000 miles per year. You probably would never operate your vehicle for 50,000 miles without changing or even checking the oil.
Increased utilities
Soot buildup occurs when the fuel to air ratio of a boiler is not correct. In addition to being very dangerous, it is also an energy hog. Soot has 5 times the insulating value of asbestos and thus, will greatly impede the heat transfer of the flue gases in the boiler. An 1/8” of soot on boiler tubes will increase energy use between 8-12%. In addition, the accumulation of soot inside a boiler and the flue could create a hazardous condition. A local school had soot build inside the boiler and flue. The soot caught fire and ruined the flue and melted the asbestos floor tiles in the classroom above the boiler room.
Scale formation is usually caused by excessive makeup water which introduces hardness into the system and usually due to system leaks. A mere 1/32” of scale buildup will reduce boiler efficiency by 2%. In addition to energy costs, the scale will cause uneven heat transfer of the heating surfaces which could leak to stressed metal and more leaks. Scale forms on the hottest surfaces so the parts of the boiler closest to the flame will have the greatest scale formation. A water softener is often used for steam systems to reduce the chance of scale.
Is it Leaking?
I like to use a water meter on the makeup water to the system to monitor water usage by the system. It should be monitored and recorded regularly. If the usage starts to increase, it would mean leaks. System leaks are the biggest boiler killers. It is common to lose a small percentage (10-15%) in a steam system because it is open to the atmosphere. The hydronic system should have no leaks. A leaking system could also increase the water treatment usage and cost.
Water Treatment
Water treatment is crucial for the safe and proper operation of a boiler. It helps avoid scale, maintain the proper pH, and limit oxygen pitting. Any of the factors could cause a leak, inefficient operation, or premature equipment failure. I urge the implementation of a water treatment program for every boiler we sell with an organization that specializes in water treatment. A local college decided to purchase the water treatment chemicals from the same company that sells soap to them. They sold the facility director on the idea of a descaler to clean the system. It did indeed clean the system and caused about a mile of pipe to suddenly start leaking and ruined two of the three boilers. The chemical treatment attacked the rubber gaskets between each section of the boiler. On another project, the treatment company did not realize the boiler was aluminum and the chemicals attacked the aluminum heat exchanger and ruined the boiler which was only a few years old. It is always a good idea to use a professional that specializes in water treatment.
Your Reputation is on the Line
The thirty-year-old steam boiler for the church finally died. The replacement boiler was installed and the equipment funding was provided by a generous benefactor. The design for the new system was donated by an engineer who was a member of the congregation. The board thought they would not have to worry about the boiler for another twenty to thirty years. The designer and the installer both recommended a maintenance and water treatment program to protect the new boiler which would have cost about $500.00 per year. The board had no money for maintenance and the boiler was left to operate on its own and ignored. The new boiler only lasted about 5 years because the system had leaks and excessive makeup water.
The board blamed the failure on the designer for choosing the boiler, the equipment manufacturer, and the installer rather than the real cause, lack of maintenance. A 2nd replacement boiler had to be installed for a cost of $25,000. If they had spent the $500 per year, they would have avoided the $25,000 replacement cost.
Life Costs
If you consider the above costs for the church, the maintenance and water treatment program would have cost the owner $500.00 x 5 years = $2,500.00. Instead they spent ten times that amount for another replacement boiler. I have seen this happen time after time when the maintenance is not done.
Chaos Factor
As you know, the equipment always fails at the worse time. We joke about getting service calls at 4:00pm on a Friday afternoon. By the time we arrive and diagnose the problem, the supply houses are closed. This leads to chaos in our company as well as the facility. Another factor which adds to the chaos is boilers always seem to fail on the coldest days and never in the summer. This leads to overtime and higher equipment and labor costs due to the outside temperature. A proactive maintenance program could limit those accidents and repairs can be planned and budgeted.
Will it take a catastrophe?
While increased energy and replacement costs by inadequate maintenance procedures are substantial, I am more concerned with the safety of the equipment and the people inside the facility. If something as simple as a filter is plugged on a furnace, the airflow is restricted and could cause a crack in the heat exchanger, allowing deadly carbon monoxide leakage into the building. When you consider a boiler, ignored safety controls could cause a catastrophic accident. A study I read several years ago showed a 2,000,000 Btuh cast iron boiler had the explosive equivalent of 32 pounds of dynamite. The study further stated a horizontal water tube boiler would have the equivalency of 10 pounds of dynamite. You would not want to be anywhere close to that boiler room if either exploded. It seems like the only time we make a change is when an accident occurs and I hope we can see the value of maintenance before an accident happens. The leading cause of boiler accidents is lack of or improper maintenance. The industry is slowly changing and the ASME CSD1 code is evidence of that.
ASME CSD1
If your locale follows ASME CSD1 code, the boiler owner is required to perform maintenance on the boiler. ASME CSD1 code covers commercial boilers with inputs between 400,000 to 12,500, 000 Btuh. The following are some of the requirements of ASME CSD1-2012.
CM-110 Since the effective operation of all safety devices depends upon their ability to respond to their activating impulses, a systematic and thorough maintenance program shall be established and performed. It further states and requires:
b) operability and set points on all devices, where applicable, shall be verified by periodic testing, and the results shall be recorded in the boiler log, maintenance record, service invoice, or other written record.
c) Any defects found shall be brought to the attention of the boiler owner and shall be corrected immediately.
CM-120 states the qualified individual performing inspections and tests shall be trained and familiar with all operating procedures and equipment functions and shall be capable of determining the equipment is in an as-designed operating condition.
Accident Causes
The majority of all boiler accidents, 43%, are the result of operator error or improper maintenance. The second leading cause of boiler accidents, 31%, is due to the low water cutoff. Nearly all boiler accidents can be avoided by simply maintaining the boiler.
Who Does the Maintenance?
Who is responsible for the maintenance of the boiler and the peripheral equipnent? Each boiler has daily or weekly tests the manufacturer recommends to be done. The people responsible should be properly trained how to operate the equipment. Since many facilities cannot send their staff to the factory for training on their equipment, the following are some suggestions to help them understand their system.
If you are the designer or installer, arrange to have the startup instructions given by the startup company to be recorded and give a copy to the owner for yearly review. This will help refresh the onsite personnel on what is required.
Be sure the customer has a copy of the Operation and Maintenance Manual. The owner could review the manual to answer some of the common questions.
Encourage the employee to accompany the service technician during a service call. In this way, they will be able to better understand the system and recognize when the system is not operating properly.
Proper Startup
When the boiler is replaced in a commercial building, it is usually completed in the summer and the startup is done at the conclusion. When a boiler is started, the building is usually under light load. It is difficult to properly adjust the fuel to air ratio because the boiler loop heats quickly and shuts off the boiler. I urge designers and installers to arrange for a follow-up visit by the startup company once the heating season is in full gear. If the startup technician returns once the temperatures drop and the installation crew is gone, the technician can test the boiler under more realistic conditions. To properly adjust the fuel to air ratio, the burner should operate for at least 15 minutes to allow the flame to stabilize. This cannot happen when the burner short cycles. In addition, the tech could verify the boiler is operating correctly. I have seen projects where contractors on site after the boiler startup stepped on the burners and burner linkages and changed the fuel to air ratios.
If you are designing or installing a boiler for your customer, encourage them to perform maintenance on the new equipment. Help them understand it is an investment and not a cost.
A properly maintained boiler will last decades. It is in everyone’s best interest to be sure the heating system is working properly and safely.
Would you like to learn more from Ray? Check out his seminars and books.
Leave a comment
Related Posts
I had written a story for Plumbing & Mechanical a while back about a fella in Canada who sent me this email: "Our problem is that five out of hundreds of univentilator co...
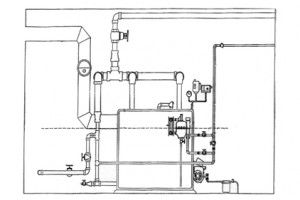
I love all the advances taking place in the world of hydronics, but I’m still seeing plenty of steam systems out there in our older cities, so knowing about dry steam wil...