This all-technical, three-hour seminar will make you familiar with the many types of old steam heating systems and what goes wrong with them. Dan Holohan’s easy-to-follow...
Steam Piping and Pressure Differential
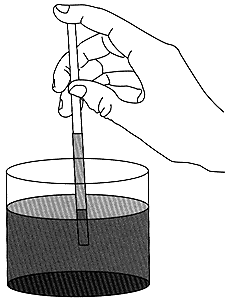
A New York City contractor called me a last winter to tell me about a situation that he had gotten himself into. We’ll call him Augie because that’s close enough.
"The old steam boiler was up on this pedestal," Augie told me. "The new one, I put down on the floor because that’s where the engineer wanted it."
"You know why it was up on the pedestal, don’t you?" I asked.
"Yeah, it was up there because this used to be a gravity-return system. I’ve seen plenty of these jobs. The boiler water line needs to cover the return lines that come down from the ends of the one-pipe steam mains. Those return mains run along the floor of the lobby. They dip under all the doorways. The boiler was up on a pedestal to make sure that those lines were always about a foot under water. That way, the steam couldn’t get into them and cause a racket."
"Very good," I said. "So why did you put the new boiler down on the floor?"
"Because that’s where they engineer wanted it," he said simply. "I have a difficult time arguing with engineers."
"Did you mention to the engineer that when the new boiler went down on the floor all those wet returns were going to turn into steam lines. Did you tell him that condensate would gather in all the places where the new steam lines dipped under the doorways?"
"I tried," Augie said. "But he told me that he was specifying a boiler-feed pump and that that would take care of everything."
"But the boiler-feed pump opens up the return line to the atmosphere," I said.
"The steam is going to work its way right into that receiver. And it’s going to be knocking around in the condensate that’s gathering under all those doorways. High pressure goes to low pressure. Right?"
"I know that," Augie said. "But the engineer told me not to worry about it because he was also specifying a big float & thermostatic trap. He had me put it right at the inlet of the boiler-feed pump."
"Did you tell him that it wouldn’t work because of the dips under the doorways?" I asked.
"Who am I to argue with a college man," Augie asked. "Besides, I figured I could kill ‘em afterwards on the extras."
"And did you?"
"Yeah, I took my pound of flesh," Augie said.
"Did you build a false water line down in the boiler room?" I asked. "That would have put all those wet returns under water again, and he still could have had his boiler-feed pump."
"Nah," Augie said. "I told him that the only way we could get rid of the water hammer was to trap the ends of each steam main."
"You get a bigger extra that way, Augie?"
"Uh huh," he said.
"So what’s the problem?" I wondered.
"I got water hammer up the wazoo! And it’s coming from the supply lines, not the return lines. Now, the whole ball of wax is sitting in my lap. The engineer is saying that things are worse now than they ever were before. And it’s all because I added those end-of-main traps. The system hammered before with his big F&T trap at the inlet to the feed pump, but he doesn’t want to talk about that anymore. He’s insisting that I created the whole problem, and he’s saying that it’s now my responsibility to make the system work."
So we talked about this for a while. I was at a disadvantage, of course, because I could only see the job in my mind’s eye. All I could do over the phone was ask questions, try my best to visualize the situation, and offer possible causes and solutions. Augie was pretty open-minded, and that was good. I often talk with troubled contractors who don’t want to consider any solution that might involve an expense on their part. "Maybe the boiler’s too small," I’ll suggest. "That’s impossible!" the guy will shoot back, not willing to check the math because he’s afraid that this may indeed be at the root of his problem. It’s like ignoring cancer.
"So, what are you hearing when the system runs?" I asked Augie.
"Water hammer," he said. "I told you that."
"But I mean when does it happen. At the start of the cycle? During the cycle? At the end of the cycle? It’s easier to diagnose if we know when."
"I get it," Augie said. "Okay, it’s like this. The boiler starts up. The zone gets hot. Then the new zone valve closes. The engineer had me install zone valves on the mains. I forgot to mention that. Anyway, when the zone valve opens again, that’s when the hammering starts. Plus, I’m noticing that the boiler’s talking on a lot of feed water. And when the condensate returns to the feed pump, the receiver overflows. I think the receiver may be too small, but if I say anything about it, the engineer will probably blame me for that too."
I was seeing all of this in my mind’s eye. Try to picture it with me. When the system starts, the zone valve is wide open, and so is the thermostat inside the F&T trap at the end of the main. The pipes are filled with air, thanks to atmospheric pressure. The steam comes through the zone valve and pushes the air through the F&T trap and into the boiler-feed pump’s vented receiver. The zone valve closes, and so does the thermostat inside the F&T trap. With me so far?
Okay, now the condensate starts to enter the main from the one-pipe steam risers. The trouble, though, is that there’s no pressure other than atmospheric pressure inside that main. That’s because the zone valve is shut. So we have atmospheric pressure on the inlet side and the outlet side of that end-of-main F&T trap. Can you visualize it?
Now, ask yourself how condensate can move across that F&T trap when there’s hardly any difference in pressure from one side of the trap to the other. Without the all-important delta-P there can be no flow, right?
So the condensate flows down from the radiators in that zone and backs up into the main and the risers. It’s trying to gather some height and some static weight so that it can open that F&T trap. Meanwhile, the feed pump is feeding the boiler, because the boiler keeps making steam for the other zones.
And then our big zone valve opens. And when it does, Mr. Steam meets Mr. Condensate in this long horizontal steam main, and their meeting is quite raucous. And then the condensate that had been stuck on the inlet side of the F&T trap comes crashing down into the feed pump receiver and floods it.
You know, it’s all about the atmosphere when you come right down to it. Put a straw into a glass of water. Hold you finger over the top of the straw. Lift the straw out of the glass. The water stays in the straw. How come? Because of the atmosphere, right?
We learned that when we were still little kids, didn’t we?
Put some water into a pipe. Hold your zone valve over the end of it. Close the other end with your F&T trap. Now, try to get the water to flow out. It won’t, will it? How come? Because of that darn atmosphere! It seems to be everywhere.
I had Augie run a half-inch steam line over the top of the zone valve. That line bled through enough pressure to make the condensate flow through the F&T trap. It’s an old trick that a guy once taught me in a dark New York City basement. Augie did what I suggested and the problem went away. Sure it cost him a few bucks, but he learned something he’ll never forget.
And he refused to share it with the engineer, of course.
Leave a comment
Related Posts
We always have turkey for Thanksgiving. I mean who doesn’t? My job wasn’t to cook it, though; it was to eat it.
I had written a story for Plumbing & Mechanical a while back about a fella in Canada who sent me this email: "Our problem is that five out of hundreds of univentilator co...