In this presentation, Gary Klein shares important information about air source heat pump water heaters (HPWH), with particular attention paid to where the warm air comes ...
Oxygen-Diffusion Corrosion in Radiant Heating Systems
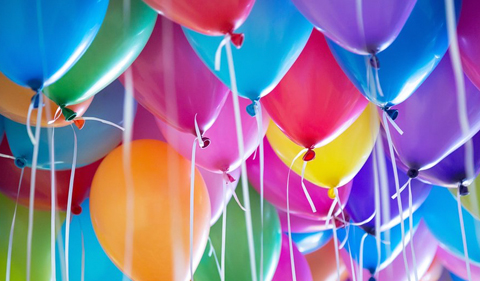
Whether you’re doing radiant floor heating or hydronic snowmelt jobs, it pays to give lots of thought to this oxygen-diffusion corrosion business. Since this is one of those areas where the marketing and the engineering can get mixed up, it pays to go back to basics, so here goes.
Too much oxygen is bad for any hydronic system because it corrodes the iron and steel. You know this is true if you’ve ever lived with a boiler relief valve that keeps popping off. The oxygen in the cold fill water comes out of solution when the boiler fires and goes to work on the metals that are lowest on the metallurgical totem pole. Usually, the iron gets the worst of it. In plain English, we call this rust. You know rust, right?
Anyway, oxygen makes metals that are ferrous (that means made of iron or steel) rust. The more oxygen there is, the worse the rusting will be. Now here comes the spooky part. The wrong sort of hydronic radiant tubing can allow oxygen to pass right through it – even if it’s buried under concrete floor, a driveway, or a sidewalk. This phenomenon has nothing to do with the pressures in the system. You could have 100-psi water pressure inside the tubing and the oxygen will still get in – if it’s the wrong sort of tubing.
Now, you may not be an engineer, but you don’t have to be to understand this. I know you’ve seen a balloon or two in your day. You probably had a few at your last birthday party. Maybe you bopped one up in the air at that rock concert you went to. Balloons have more pressure inside of them than they do outside of them, right? But why do they go flat after a few days?
And how come those Mylar balloons take a lot longer to go limp? You know the sort I’m talking about? The shiny silver ones that have things like, "Over the Hill," and "Happy Birthday You Old Fart" printed on them? How come they last longer? It seems that some materials do a better job of holding gases than others, eh?
And therein lies the great answer to how the hydronic radiant tubing sucks up the oxygen. It has nothing to do with the pressure of the liquid, it has to do with the concentration of the gas we call oxygen. Mother Nature likes to balance things, and if she finds more air molecules inside an ordinary balloon than she finds outside, she will move the air molecules right through that old balloon. She can do this because an ordinary balloon is a semi-permeable membrane. That’s a fancy way of saying there are tiny holes in the balloon. These holes are so tiny that liquids can’t pass through them, but gases can. If you filled that balloon with water instead of air, that balloon would stay filled until you tossed it.
Now, follow this. When you fill a heating system with cold water, the oxygen that leaves the heated water will react chemically with the iron and steel in the system. The reaction eats up the oxygen and forms a compound called iron oxide. Iron oxide, in plain English, is rust. It’s the black stuff you see suspended in the water. The longer you can leave water in an all-metal heating system (one without plastic or rubber hydronic radiant tubing) the better it gets. That’s because once the oxygen reacts with the ferrous metals and forms iron oxide, the corrosion stops. That nasty, stinking, black water is like fine wine to a hydronic system. It’s the good stuff. And as long as you don’t keep adding more fresh water, you will have no more corrosion.
So here’s where the tubing comes in. As soon as the oxygen burns itself up, chemically speaking, the water inside the system finds itself in oxygen deficit. In other words, there’s more oxygen in the air that’s outside the tubing than there is in the water that’s inside the tubing. Since the tubing is a semi-permeable membrane, Mother Nature begins to shove oxygen molecules through the wall of the tubing and into the water. And that causes more corrosion. If this goes on long enough, you wind up with this sludge (rust) that flows around with the water, messing up anything that has a close tolerance to it, such as a control valve or the business end of a circulator. The oxygen also loves to go to work on the thin steel in a diaphragm-type compression tank. Oxygen won’t usually damage a cast iron or steel boiler because most of these boilers have relatively large passages. The flow of water, however, will carry away the sludge and dump it in places you never even knew your system had, and that’s why oxygen-diffusion corrosion is something you need to avoid.
Now, you should know that temperature plays a part in this. Generally, the hotter the water is the worse things get. If you keep the temperature below 140 F, the corrosion doesn’t show itself in such a dramatic way. And since most slab installations will have the temperature of the water down around 110 degrees F, or so, oxygen-diffusion corrosion is less of a big deal. The jobs that will get you, though, are those staple-up jobs because the water will be hotter here, as it will be on those snowmelt jobs.
But let’s get back to those balloons for a minute. How come the Mylar balloon doesn’t lose its air so readily? And have you ever noticed when you’re eating a bag of potato chips that the bag you’re holding looks a lot like a deflated Mylar balloon?
What you have in your hand, my friend, is an example of an EVOH, which stands for a very long word I will not get into right here. An EVOH is a material that does not readily let gases through. Air can’t easily get in or out. That’s why the expiration date on the potato chips is something like 2055. It’s also why your Mylar balloon hangs around your ceiling so long. This material is not a semi-permeable membrane.
Hydronic radiant tubing manufacturers use an EVOH that’s similar to Mylar on their tubing to keep the oxygen from working its way into the water. Lately, some manufacturers have switched to a thin layer of aluminum, which they sandwich between layers of either PEX or rubber. Aluminum is a really good oxygen-diffusion barrier because it is a metal. Gases will not pass through metal. A balloon made from aluminum may not be practical, but it will never deflate.
If you use tubing with an oxygen-diffusion barrier such as aluminum or an EVOH coating, oxygen will not enter the tubing and you will not have any abnormal corrosion. The controversy that took place during the early Nineties revolved around the accusation by some manufacturers that other manufacturers made tubing that did not have a suitable oxygen-diffusion barrier. They based their accusations on something called the DIN Standard. DIN, loosely translated, stands for Deutsche Industry Norm, the "Deutsche" being the Germans. Some of the folks who were selling hydronic radiant tubing in America back then adopted DIN Standard 4726. This standard demands that hydronic systems not allow in any more than one-tenth of a milligram of oxygen, per liter of water, per day, when the water is 40 degrees Celsius (104 F). In case you’re wondering, this is an extraordinarily small amount of oxygen. Nowadays, every tubing manufacturer has a product that will meet DIN4726, but that wasn’t the case in the early Nineties, thus the controversy.
But having a tubing that meets DIN4726 isn’t the only way you can protect a hydronic radiant or snowmelt system from oxygen-diffusion corrosion, and tubing manufacturers who weren’t meeting the strict German standard were very vocal about this. You see DIN4726 doesn’t demand that you do it a certain way; they just say DO IT! And you can do it in a couple of other ways.
First, you can separate the ferrous (iron and steel) parts of the system from the nonferrous parts of the system by using a stainless steel heat exchanger. The most popular are the braised-plate exchangers. Those are those tiny ones that look like silver bricks. They keep the water in the plastic or rubber tubing isolated from the steel and cast iron parts of the system, and they’re perfectly acceptable.
You can also install a system that has no iron or steel in it, of course. Brass valves and circulators, copper boilers – these will do nicely because these materials won’t rust. Copper boilers are also very popular with snowmelt systems because they allow you to use non-barrier tubing and thus lower the cost of the installation.
Another way to prevent corrosion and meet the standard is to add corrosion-inhibiting chemicals to the system water. The trouble with chemicals, though, is that you have to monitor them from year to year because they lose their potency over time and can actually cause corrosion. In Europe, where everyone is very concerned about the environment and pollution, contractors avoid chemicals because there are few places to dump them when it’s time to get rid of them. And that’s why you find so much oxygen-diffusion-barrier tubing in Europe. When those European tubing manufacturers began to market their goods in North America, they didn’t want contractors considering chemicals or heat exchangers as a viable option to what they were selling. I’m sure you can understand why.
Nowadays, literally every tubing manufacturer marketing in North America sells a tubing that meets DIN4726. What’s fun to watch, though, is how some of them are now encouraging American contractors to use heat exchangers or chemicals and non-barrier tubing, which they offer at a lower price. Why would they do this? Because this tubing is less expensive! It gives them a better shot at the job.
So there you have it in a nutshell. Is oxygen-diffusion corrosion a real concern? Yes, but mainly on systems where the operating temperature is above 140 F (staple-up and snowmelt systems). Should you protect every system you install by using either DIN-Standard tubing, a heat exchanger, or corrosion-inhibiting chemicals? Absolutely! It’s all basic science and it’s as close to you as that next bag of potato chips or that big red party balloon.
Leave a comment
Related Posts
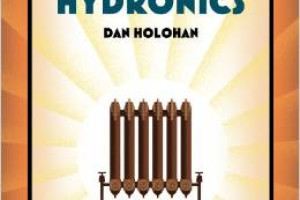
In this all-technical three-hour seminar, Dan Holohan will give you a Liberal Arts education in those Classic Hydronics systems. He’ll have you seeing inside the pipes as...
We always have turkey for Thanksgiving. I mean who doesn’t? My job wasn’t to cook it, though; it was to eat it.