In this presentation, Gary Klein shares important information about air source heat pump water heaters (HPWH), with particular attention paid to where the warm air comes ...
Radiant Heat and Wood Floors
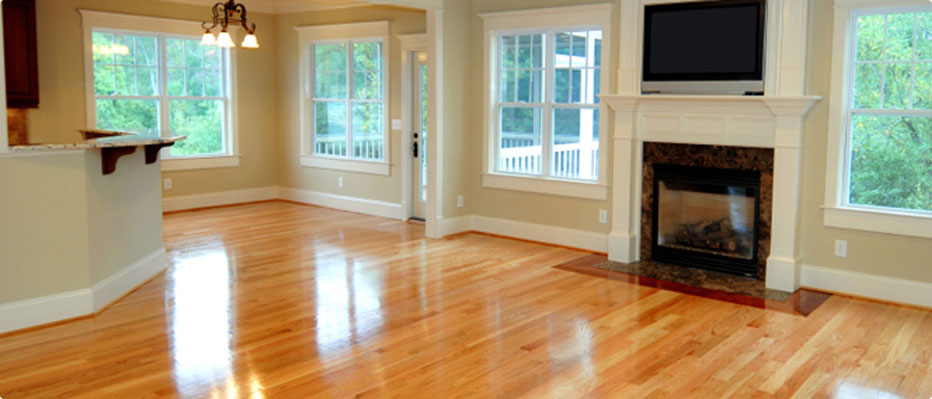
More and more radiant systems going into existing homes as retrofit projects. On many of these jobs the tubing winds up getting attached to the underside of the wood floor. On other jobs, the tubing goes down on top of a subfloor, beneath the finish wood. The tubes may be in concrete, or they may just be sandwiched between the subfloor and the finished floor. To avoid problems, there are certain rules you should follow when you’re working with any radiant floor that involves wood. Here they are.
The wider the boards, the greater the chance for trouble. Try to stick with boards that are no wider than three inches. Wide wood is much more likely to warp warp. I’ve been on jobs where the floor warped so much it looked like it was made out of corduroy (they all had wide boards). Keep this in mind – especially if you’re doing retrofit work.
Use mechanical humidity control. Ideally, the relative humidity in a radiantly heated home that has wood floors should be no more than 50 percent. "Without this constant humidity, you must live with the cracks in the wood," according to the experts at the National Oak Flooring Manufacturers Association. Understand this before you begin, and don't be surprised when the cracks show up if the humidity isn't what it should be.
Realize that the seeds of the damage on any job will be planted during construction. If you’re placing wood over a concrete floor containing radiant tubing keep in mind that it takes time for the water to leave the concrete. And as the concrete dries, the moisture will leave it and enter the wood. As a precaution, tape a square of clear, plastic sheeting over the concrete floor and watch it carefully for moisture. Don’t let the carpenters install the wood flooring over that new heating system until the plastic proves there’s no moisture left in the concrete.
Provide for heat and ventilation during construction. You have to do this because the painters and plasterers are adding gallons of moisture to the indoor environment. If you don’t get rid of it, all that water is going to wind up in the wood floor. The damage won’t show up until you turn on the system. And by that time, the other guys will be long gone.
Buy a moisture detector. Spend a hundred bucks or so and get your own. It’s a great tool to have if you’re doing radiant heating systems. Stick the detector in the wood and you’ll immediately know what’s going on. Keep a log of the finish wood’s moisture content as the job progresses. You’re aiming for 6% moisture, at most, before you turn on the heating system under that new wood floor.
Run the heating system for about five days before you let the carpenters install the finish wood. This will help dry out the wood. I remember visiting a famous movie actor’s home in Park City, Utah while it was still under construction. The finish wood sat in the corner on a pallet as the radiant floor ran wild and uncontrolled in the subfloor’s gypsum concrete. It must have been 90 degrees F in that house and they hadn’t even installed all of the windows yet! This was in late October, by the way. That wood was pretty dry before they nailed it in place! If you find you can’t run the heat beforehand, lay down an 8-mil polyethylene vapor barrier between the concrete or gypsum-concrete and the wood. That should keep the wood from sucking up the water.
Avoid using any paper containing tar or horsehair under the wood floor. These things can give off an odor when the heat comes on. And the smell can stay with you for a long, long time. Use red resin paper instead, and if you’re doing a retrofit, under-the-floor job drill up through the floor to check for that tarpaper or horsehair.
Never make a wood floor hotter than 85 degrees F at its surface. Even if rugs are going down. Too much heat isn't good for the wood. Consider using a setpoint control to monitor the wood’s surface temperature instead of an air-temperature thermostat. You may have to have some sort of supplemental heat in the room if an 85-degree surface won’t get the job done on those really cold days. Whether or not you’ll need this depends, of course, on the room’s heat loss and the size of the floor.
Summertime means more humidity. After that first summer, when the system you installed kicks in, the finish wood just might develop small fissures. That’s normal. Just know that it's liable to happen.
And about those small gaps that may appear in the floor. This can happen when there’s a urethane finish on the floor and the floor is made from nonlaminated solid wood. The finish actually "glues" the individual boards together, and as the wood expands and then contracts, the contraction will localize itself and wind up as a gap. This is so common with hardwood floors (whether they have hydronic radiant heat under them or not) that the hardwood flooring industry even has a name for it. They call the phenomenon, "panelization." Be aware of it before you start the job.
Learn more about wood. Go right to the source and learn more from the wood-floor associations. These folks provide brochures some very interesting brochures: National Oak Flooring Manufacturers’ Association, Inc.
Leave a comment
Related Posts
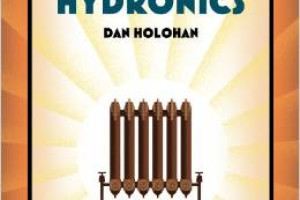
In this all-technical three-hour seminar, Dan Holohan will give you a Liberal Arts education in those Classic Hydronics systems. He’ll have you seeing inside the pipes as...
We always have turkey for Thanksgiving. I mean who doesn’t? My job wasn’t to cook it, though; it was to eat it.