In this presentation, Gary Klein shares important information about air source heat pump water heaters (HPWH), with particular attention paid to where the warm air comes ...
Old Houses, Old Systems
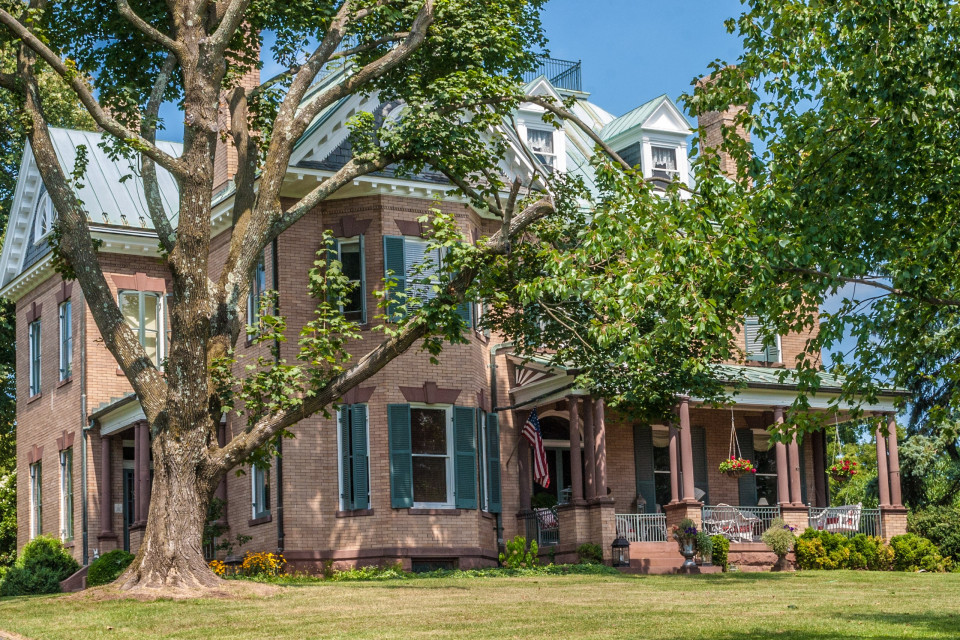
One of the things I love most about this business is the history of the heating systems in the old homes we work in. I enjoy poking around in the basements of old homes trying to figure out century-old heating systems. I wonder what my counterpart was thinking when he designed and installed the heating systems in these old homes as I attempt to apply modern heating technology to these ancient hot water and steam systems.
There are plenty of old and historic homes and buildings in the Washington, D.C. metro area, where I work. We recently had the privilege of updating two heating systems in historic homes.
Turn of the century Victorian
The first system was a lovely, old Victorian located in Leesburg, Va. It was built in 1899, and is listed on the National Register of Historic Places. I first met the owners of the home back in the early 90s. They were having problems with their heating system. Their existing cast iron oil boiler was cracked and leaking. I noticed another fairly new boiler block sitting in the corner of the basement. Whoever replaced the boiler did not bother to remove the old carcass. What was causing the sections to fail prematurely?
The original Gurney coal-fired boiler was still in place but valved off (see photo below). The heating contractor riveted a steel plate to the boiler. It read, simply, “Hubbard Heating Co. Washington, D.C.” The owner wanted to leave this boiler in place for historical value. I surveyed the heating system trying to figure out why two boiler blocks would fail in short order. This was an old gravity hot water system with massive cast iron radiators and large 3-inch and 4-inch steel mains. There was an old riveted steel expansion tank in the attic with the overfill pipe stubbed through the roof.
I marveled at the 4-inch mains that someone cut and threaded by hand 100 plus years ago. The pipes were meticulously pitched for gravity flow and carefully secured with steel pipe hangers. When the house was built in 1899, electric lighting was in its infancy. The house had both electric wiring as well as gas lamps. The 3/8-inch gas lamp piping was still visible throughout the house, and several gas lamp fixtures were still mounted on the basement walls.
The new oil boiler was piped direct to the supply and return mains. It was readily apparent what caused the block failures. The original coal boiler gravity system heated slowly through natural convection, as there was no pump on the system. The new cold-start oil burner would fire on a call for heat and kick on the circulator pump. Huge quantities of cold water would flow back to the boiler causing the cast iron to crack from thermal shock. In addition, the sections were severely sooted up due to prolonged firing at low block temperatures.
I replaced the boiler with a Burnham V-7 oil boiler and piped in a thermal bypass to temper the cold return water. I also used a low head, high flow three-piece B&G Series 100 pump to mimic the gravity flow. This system lasted almost 20 years, until the client decided to upgrade the system and convert from oil to gas. It was still fully functional and operational when we took it out of service.
The replacement system consisted of a Triangle Tube Prestige condensing natural gas boiler. We also replaced an electric water heater with a Smart 80 stainless steel indirect fired DHW tank (see photo below). Because of the low head loss of the system, I piped the supply and return directly into the boiler without a low loss header or primary/secondary piping we would typically use with this type of boiler.
In this case, the goal was to maximize the combustion efficiency of the boiler by returning the lowest temperature return water back to the boiler. Flow is not an issue, due to the low pressure drop of the large mains and radiators. This is a perfect application for condensing boiler technology. These boilers operate most efficiently at low temperatures. This system operates on a reset curve with a maximum temperature of 160°F at design conditions.
This past winter was the second winter the new system has been in service. The owner reported improved comfort with significant fuel savings over the oil boiler system it replaced, in spite of the record cold winter this past season.
Civil War-era home
The second project was in an Italianate farmhouse built in 1860. The house is located in Thurmont, Md., about an hour north of the city, and is still in the same family as the original owner. The house was originally heated with fireplaces and had no central heat.
The current owner’s grandfather was a steamfitter and installed two steam systems in the 1940s. He installed two Kewanee steel oil-fired boilers connected to one-pipe steam systems (see photo below).
The system featured a combination of column-style cast iron radiators and convectors that he fabricated/welded in his shop.
We did this job in two stages. We replaced the first boiler about 10 years ago using a Burnham V-8 cast iron oil boiler. We replaced the second boiler more recently employing a Burnham Mega Steam cast iron oil boiler.
The owner had both chimneys lined with stainless steel liners. We replaced all of the main vents, radiator vents, and a few of the valves that were broken. We ordered an optional header piping kit with the MegaSteam, which streamlined the piping process and minimized the amount of cutting and threading of black steel pipe. We ordered the boiler with an optional tankless coil to feed an aqua-booster tank in the winter. In the summer, the client closes a valve and uses the electric element in the tank for DHW.
It is always a challenge matching current heating technology to these old systems. In this case, both jobs went smoothly. The hardest part was removing the heavy steel Kewanee boilers from the basement.
I cringe when I see these old systems ripped out and replaced with gas forced air or heat pumps. It is like ripping the heart out of these beautiful old structures. While sometimes difficult and challenging, I would much prefer to restore the heating systems to their former glory, the way the original heating engineers intended them to be.
Dan Foley is president and owner of Foley Mechanical, Inc. based in Lorton, Virginia. (www.foleymechanical.com). FMI specializes in radiant, hydronic and steam systems as well as mechanical systems for large custom homes.
Leave a comment
Related Posts
This all-technical, three-hour seminar will make you familiar with the many types of old steam heating systems and what goes wrong with them. Dan Holohan’s easy-to-follow...
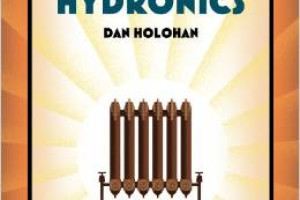
In this all-technical three-hour seminar, Dan Holohan will give you a Liberal Arts education in those Classic Hydronics systems. He’ll have you seeing inside the pipes as...