This all-technical, three-hour seminar will make you familiar with the many types of old steam heating systems and what goes wrong with them. Dan Holohan’s easy-to-follow...
A Bit About Vacuum Pumps
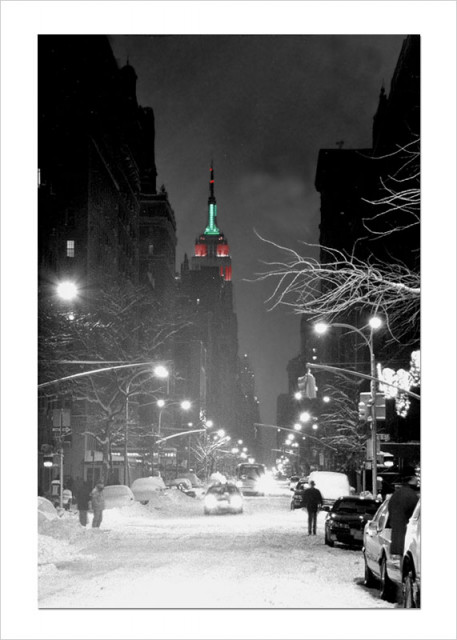
Steam systems that make vacuum with pumps have been around for more than 100 years. In 1899, D.F. Morgan wrote an article in The Metal Worker magazine, suggesting that designers skip the pump and let the steam make its own vacuum by expanding when it formed, and contracting when it turned back into condensate.
He wanted to take advantage of the 1,700:1 expansion ratio between water and steam. The trick was to make all the pipe joints tight so that air couldn’t get back into the system once the steam had shoved the air out, and to use special air vents that had check valves at the outlets. When steam turned into condensate and shrank, you’d wind up with a naturally formed vacuum and water would then boil at a lower temperature. This took advantage of the lower Btu input of a coal pile that was burning down as the hours went by.
These systems worked well, but only on coal-fired systems. When we started using oil and natural gas instead of coal as a fuel, these systems became automatic. A thermostat started and stopped the burner, and when the fire stopped, there wasn’t as much residual heat left in the boiler (compared to coal, that is). The vacuum formed quickly, and that was the problem. Not all the air escaped from the system on the first firing cycle, and when the vacuum formed, that air expanded tremendously. It moved out of the radiators and down into the pipes, stopping the steam from reaching up to where the people were (where there is air, steam will not go).
So when the fuels became automatic, the vacuum vents on the radiators and near the ends of the main became a problem. The Dead Men removed them. Or at least they were supposed to remove them. If you have an oil- or gas-fired steam system and it has this type of vacuum vent, replace those vacuum-type vents with standard air vents and the system will balance better.
There were some other systems that used mercury-filled devices to make vacuum. Trane was one company that made such a device. It allowed the expanding steam to push the air through the pipes and the radiators and then into a tube that dipped into a pot of mercury. The air would bubble up through the mercury, and when the steam collapsed back into water, air couldn’t reenter the system through the mercury pot. It worked beautifully with coal, but if you should come across one of these antiques, be careful with it. Mercury is no longer something we should be rolling around in our hands, as we did when I was a kid. Who knew?
Vacuum systems that used pumps to make the vacuum have been around even longer than the naturally induced systems I just described. You’ll see vacuum pumps on big jobs, such as the Empire State Building. The advantage of having a pump is that it increases the differential pressure across the system by lowering the return-side pressure. That allows you to design with smaller pipes, valves and fittings.
Typically, a vacuum pump runs between 3- and 8-inches of mercury vacuum. It tries to maintain an average of 5-1/2 inches. Two inches of mercury vacuum is equal to one-psi of positive pressure, so when you add the positive boiler pressure to the negative vacuum pressure, you get the total system pressure differential. If the folks in the Empire State Building run 3-psi steam pressure on a frigid day in February (which they do), and the vacuum pump is maintaining about 3-psi negative pressure (or about six-inches of mercury vacuum) the system will have a 6-psi pressure differential from supply to return. That’s gets the steam to where it needs to be.
Now think about what happens when the vacuum pump fails in a big steam-heated building and the people in charge decide not to have it repaired because it costs too much. Suddenly, all of their pipes, valves and fittings are undersized because the pump isn’t there to help pull the air through the pipes. The steam now has to do all the work of pushing that air, but the pipes are too small for that; they put up a lot of resistance. The steam slows down and some of the tenants have to wait a long time for their heat. And while they’re waiting (and complaining), other tenants are getting too much heat. These people are opening their windows. The person in charge of the boiler will no doubt raise the boiler pressure to satisfy all the tenants, but this just burns more fuel.
Crazy, isn’t it? We’re now burning more fuel to heat a building that has its windows open.
So we can say this for sure: Once it’s a vacuum system, it’s always a vacuum system. This is because the Dead Men sized every pipe, valve, fitting, and steam trap in that building for a pressure-to-vacuum differential. Without the vacuum pump, nothing works as it should.
And the reason why the pump failed is probably because the steam traps failed. You have to maintain those steam traps. There’s no way around that. It’s like painting a bridge. You’re never really done when it comes to steam traps.
And by the way, the reason why they can get by with such low pressure in the Empire State Building is because the pipes are the right size for the load (and the vacuum pump is working). It’s like this:
When steam forms, it goes off like microwave popcorn. I mentioned earlier that the expansion ratio is 1,700:1. Try to see that in your mind’s eye. Imagine a pint glass, one that you’d use to hold a big, cold draft beer. It’s tapered, right? It’s wider at the top than it is at the bottom, but if we measure in the middle of the pint glass we’ll come up with about 2-1/2” in diameter.
Think of that pint glass as a pipe that we’re going to fill with steam. How tall is it? About six inches, right? It’s filled to the brim with water (the beer’s for when we’re done working). We’re going to turn that water into steam, so we’ll need 1,699 more pint glasses. We’ll cut holes in the bottom of each and stack them. Try not to let them tip.
Or we can just make it easier by just getting ourselves a pipe that’s as tall as 1,700 stacked pint glasses. That pipe would rise about 850 feet into the building, or about 85 stories. The Empire State Building has 102 stories.
Now to get one pound of water (that’s about what’s in that pint glass) from 32° F to 212° F, we need 180 Btus (one Btu raises one pound of water one degree on the Fahrenheit scale). We add the 180 Btus and we now have liquid water at 212° F. It’s not yet steam. To get the liquid to change state, to make those water molecules so excited that they just want to leap off the surface of the water and head out for the radiators, we need to add an additional (and astonishing!) 970 Btus per pound of water. That’s more than five times the amount of heat it took to get the pint of water from 32° F to 212° F, and at this point, the steam is at 0-psi pressure.
This is the stuff that heats the building, and it’s there at no pressure at all. The steam will move on its own. Add a bit of pressure (but not much) to overcome the slight pressure drop of the properly sized piping and the steam will go a very long way. Insulate the pipes so the steam doesn’t condense before it reaches the radiator and it will go further still. Put a vacuum pump on the return to create a greater differential pressure from supply to return and you can use smaller pipes, valves and fittings throughout the whole building when you’re doing the design. And if you were building that building isn’t that what you would do? I sure would. It saves a ton of money.
But if you inherited the service on that building, or some other building that has a vacuum steam system, everything is already sized and in place. And this is why you do have to maintain that vacuum pump. And the steam traps.
And the vigilance you have to pay those key components never ends.
Leave a comment
Related Posts
We always have turkey for Thanksgiving. I mean who doesn’t? My job wasn’t to cook it, though; it was to eat it.
I had written a story for Plumbing & Mechanical a while back about a fella in Canada who sent me this email: "Our problem is that five out of hundreds of univentilator co...