This all-technical, three-hour seminar will make you familiar with the many types of old steam heating systems and what goes wrong with them. Dan Holohan’s easy-to-follow...
Flooded Steam System Caused by Poor Piping
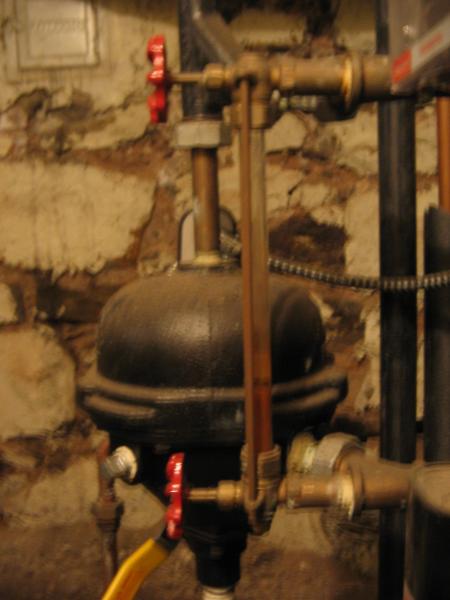
Always ask, "What can cause this?"
I once looked at a house in New Jersey where the first-floor ceiling had caved in due to a disagreement with the steam system. This was a one-pipe steam system. It had an automatic water feeder, and mechanical things can be cruel from time to time.
But don't get me wrong; I like automatic water feeders. I think a feeder provides an excellent back-up to a low-water cutoff, and I've always thought of them that way – as a back-up safety device, not as a convenience item. I figure if you sell a feeder as a convenience item, the customer will never again blow down the low-water cutoff again. He may never even go down to the basement again!
But even the best automatic water feeder can get stuck open if you don't treat it properly. And that's what happened here. The feeder didn't close tightly while the homeowner was at work. The water quickly rose to the second floor and spewed out of her radiator air vents and onto the floor.
By the time she got home, she could have used scuba gear.
Her heating company was more than cooperative. They got there quickly and looked things over, trying to figure out what had gone wrong. The boiler had been there for 11 years. The near-boiler piping was up to spec, and so was the system piping. The boiler cycled off a vaporstat, cutting in at six ounces and out at eighteen, which was fine for a house this size.
Two insulated steam mains ran around the basement. They were the right size and pitch for the connected load. The returns were above the boiler’s waterline, and every piece of pipe was visible. Nothing went under the floor and there were no water leaks or steam leaks.
The system had worked well for years, until the flood. The heating company concluded that the automatic water feeder had simply gone wrong and they replaced it with a new one. They weren't sure why the feeder misbehaved, so they chalked it up as "just one of those things." And so did the insurance company.
Everyone hoped for the best at this point, but the homeowner was worried that another flood might show up one day, so, being a friend, she called me. She wasn't going to sleep well until she knew what had caused the problem. So I stopped by and here's the rest of the story.
My approach to troubleshooting is a simple one. When I'm looking at a problem, I try not to let anybody tell me what's wrong because I figure if they knew what was wrong, I wouldn't be there. Make sense?
I like to poke around quietly for a while without asking any questions, sort of get the lay of the land. And I always try to see the system instead of just the symptoms. I begin with something that's undeniably true. That's always been important to me because troubleshooting can be like walking through a maze. It always helps me if I have a safe place to which I can return. By stating that undeniable truth right up front, I can focus real hard. In this case, the system had flooded up to the second floor, and that was undeniably true. So the next thing I did was ask myself, what can cause this? This forces me to focus on just that one point. I needed to answer that question. What can cause that much water to enter a steam system?
Everything in the system seemed fine. Everything, that is, except the way the low-water cutoff was piped. Someone had raised it a few inches to cover the tankless coil. I knew that could lead to problems in a modern steam boiler because the feeder should feed at the safe, minimum water line – not at the center of the gauge glass. If you're constantly feeding at the center of the gauge glass, the returning condensate will flood the boiler. Once that happens, the steam will yank water into the system as it heads towards the radiators, creating water hammer and uneven heat throughout the house.
But that wasn't the problem here. Surging alone couldn't flood a system this dramatically. Someone would have to repipe the low-water cutoff to where it should be, but I knew that's not what caused the flood.
The system flooded to the top floor. There was no denying that. I figured there were four possibilities:
- The feeder bypass valve had failed.
- The feeder bypass valve was accidentally left open.
- The tankless coil had a leak, and that was flooding the boiler.
- The automatic feeder didn't close when it should have.
Those are the only things that can lift water that high and that fast in a house. Surging from a too-high water line couldn't do it, so I started with the bypass valve. It looked fine. The homeowner said that she never touched it, so I let the valve off the hook and moved on to the tankless coil.
The heating company had already isolated and checked the coil for leaks, and they found it to be okay. "I don't know why it's still there, though," the homeowner said, "I don't use it anymore."
As it turns out, the coil had been abandoned a few years back when the homeowner had had a separate water heater installed. I didn't think the coil was responsible either because if it were, the boiler would flood all the time. But since it had flooded just that one time, we were left with only one other possibility – the feeder.
So I asked that key question once more time. What can cause a feeder to flood a system? I know that feeder manufacturers caution us to supply these units with cold water instead of hot water. That's because calcium and magnesium come out of solution in hot water when the temperature exceeds 120 degrees. Calcium and magnesium can form a crust on the feed valve's seat and keep it from closing tightly. The result is often a flood.
So I felt the feed line. It was cool, but it was also connected to that abandoned tankless coil. That didn't register with me at first, but as we were running the boiler to make steam I chanced to put my hand on the cold water feed to the tankless coil again. It was warmer than it had been – a lot warmer. I left my hand there for a few more minutes, and then I smiled. The cold pipe was getting hotter and hotter.
Remember, that abandoned tankless coil? No cold water will enter it because no hot water is leaving it, but it's still filled with water. And there it sits in the center of a steam boiler, surrounded by very hot water.
The cold water line got hotter and hotter. It fed back up the line and began to heat the branch to the automatic water feeder. After a while, the line to the feeder was red hot. And that's when the feeder opened. The low-water cutoff, which you'll recall was installed too high, was causing the boiler to surge. When the water line bounced, the feeder opened, and fed hot water instead of cold water. And along with the hot water came the mineral deposits.
Now I knew these feed cycles weren't enough to fill the entire house with water, but over time, it was enough to lime up the feeder seat and keep it from shutting tightly on the day the house flooded. The original feeder didn't have a built-in time delay (as the new one did). I'm sure it fed more frequently than the new one was doing. More feed cycles meant more mineral deposits on the feeder's seat.
So what did we do? We had the piping to the tankless coil cut. We didn't need that coil, so why should it stay connected? We made sure the heating company didn't cap the coil's inlet and outlet lines because that would have created a dangerous situation. We left those lines open so no steam pressure could build inside the coil. We also had them repipe the low-water cutoff to the proper feed/cutoff level.
So always ask that key question – What can cause this? Focus on that and you'll be able to solve just about any problem that comes along.
Leave a comment
Related Posts
We always have turkey for Thanksgiving. I mean who doesn’t? My job wasn’t to cook it, though; it was to eat it.
I had written a story for Plumbing & Mechanical a while back about a fella in Canada who sent me this email: "Our problem is that five out of hundreds of univentilator co...