In this presentation, Gary Klein shares important information about air source heat pump water heaters (HPWH), with particular attention paid to where the warm air comes ...
Considerations When Using Constant Circulation
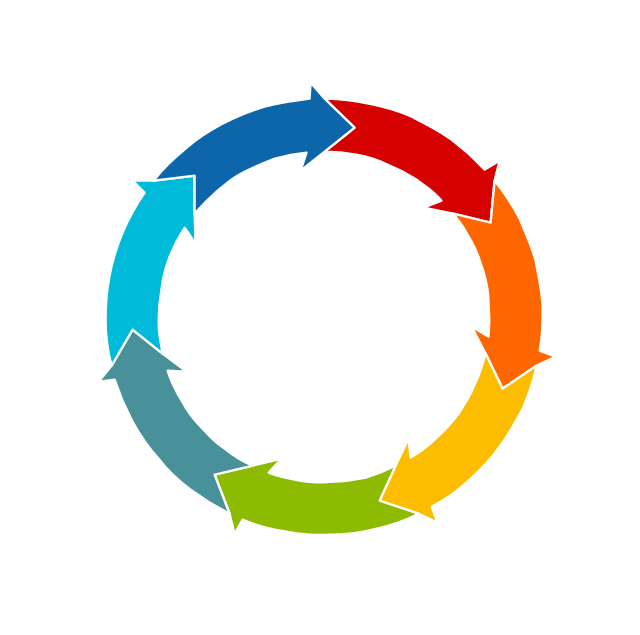
A question asked on the Wall, "What do I need to consider with a hot-water system running on constant circulation?"
Mark Eatherton replies:
It has to be designed into the system from the git go. It's not just a simple matter of having to wire a pump to run all the time. It is a European design, which incorporates some non-electric technology with some electronic technology, and throw in some hydraulic control devices (either pressure activated bypass or variable speed circulators), and you have a "system."
There should be a primary room master control sensor watching worse case scenario (north-facing room with lots of glass) to dictate supply temperature and flow requirements (this zone is called a reference zone and is the only truly "free flowing" zone).
All other zones are limited by a non-electric thermostatic operator, either at the point of use (panel radiators) or with a remote cap tube controller (large radiant surfaces).
A basic outdoor reset program is established, and either over-ridden or under-ridden depending upon what the indoor feedback loop is sending back to the master PID controller. Not all control logics are conducive to constant circ operation. Some people view it as being an easier, cheaper way to control their system, versus zone valve
operation, and this is not the intent of this design. The primary intent of this design is to provide the highest degree of comfort for the smallest amount of parasitic power consumption, all while maintaining the lowest temperature of operation possible.
Two possible logics that are compatible with this theory of operation are the two big German boiler manufacturers, Buderus and Viessmann. tekmar controls can be applied by knowledgeable persons, and I'm certain there are others out there that can be set up to work as well.
One notable disadvantage to this system is that due to its simplicity, it is not as conducive to the new Web-based control systems, whereby a person can turn individual rooms up and down from a remote location. Generally, you have the opportunity to shift the reset curve backwards by a predetermined amount (say, 20-degrees F), which would cause all thermostatic radiator valves to go wide open and undershoot most of their targets. A few days before you are ready to reoccupy the space, you'd send a signal to the logic, pushing its reset curve back to an occupied position.
Continuous circulation with outdoor-air reset control is not for everyone, just those that understand its operation and are willing to live with the nuances associated with its operation (slow reset response, lack of electronic interface etc.).
Unless you are using a WILO Stratos pump, you will need to incorporate some means of dead-headed pump protection (read pressure-activated bypass) because other than the master controller, there is no communication between the zones and the pump.
It does require a completely different mind set than the BANG-BANG North American control logic, but it ends up using less energy and provides a higher degree of internal comfort.
As a side note, I once set up the reference zone with the PAB to avoid total free-flowing that zone and shorting the other zones. It worked quite well. When all the other sub-zones were calling, little to no flow went through the reference zone, thereby causing the logic to increase the supply temperature, thereby shutting down the other sub- zones quicker, and when they were satisfied, bypass started occurring in the reference zone and it too became satisfied. I'd originally thought possibly the reference zone might cool down too much, but have had zero complaints form the persnickety occupants in six years of operation.
Mike Thies replies:
Constant Circulation with TRVs. Is it explained as simply as, when the boiler is on, the circulator is moving hot water through the loops that feed radiators?
Not quite, but if you say, "When the structure requires heat, the circulator is moving heated water", you're awfully close. Unfortunately, though, the reality isn't quite that simple.
I'm referring ONLY to systems using TRVs or FHVs in the following (this may seem elementary, but first you have to understand how TRVs operate and what they can and cannot do).
TRVs are two-way valves. Fluid goes in one side and it comes back out at any rate between "full on" and "full off." In other words, a TRV is very simply a proportional flow valve. It's the job of the TRV actuator to regulate the flow. The actuator senses temperature (usually room air) and has an adjustable scale. It regulates the degree of opening of the TRV valve body in an attempt to keep the actual room temperature just equal to the room temperature setting.
If the sensor detects that the actual air temperature is dropping below the setting, the valve is opened somewhat; if it detects a rise above setpoint, the valve is closed somewhat. Note that it typically does not fully open or close the valve; it moves the setting proportionately to the deviation between actual and desired. It generally takes a difference of about plus/minus 4-degrees F to cause the valve to fully close/open.
So, the first rule regarding TRVs is that they regulate flow. They are ONLY capable of regulating flow. While it may look and feel like they are regulating temperature, they can ONLY do this by regulating flow.
The second rule of TRVs is that since they are only capable of regulating flow and strive to maintain the desired setting by regulating this flow proportionally, that they "want" to be supplied with constantly circulating water, heated at least enough to meet the load any time that heat is required in the structure. Stop the flow of water, or let it fall too low, and the setting they're trying so hard to maintain can no longer be achieved. Room temperature will fall, and when sufficient heat is again available, the operator will be forced to open the valve quite wide. Without this constant circulation of adequately heated water, TRVs and their operators begin to resemble typical on-off thermostats and have less and less of their inherently proportional nature.
The third rule of TRVs is that they are fully self-contained. They can neither receive information from, nor provide information to, the boiler. They cannot tell the boiler "I'm satisfied," and nor can they directly tell the boiler "I need heat" or "I don't need heat." ALL they can do is regulate flow, and again from "full on" through "full off." This distinguishes TRVs from more common forms of "zoning" such as by on-off valves or on-off circulators, which do provide a control link between the boiler and the zone controller (typically a wall thermostat).
Many would stop here and say, "That's all the rules, or at least everything you need to know." But it's not ALL of the story.
While TRVs cannot directly provide control between the boiler and the emitters, they CAN provide indirect control, and not only to the boiler but to each other! How do they do this? By regulating flow through the system as a whole, as well as regulating how each TRV shares the available flow. HOWEVER, this method only works well when true constant circulation of heated water is used! ANYTIME the structure requires heat, the circulator must be running with each* emitter controlled by a TRV. (*Carefully engineered radiant panels such as bathroom floors are a notable exception provided that the supply temperature uses reset.)
So, TRVs provide proportional flow control, want constant circulation of adequately heated water, provide no direct control link to the boiler yet provide an indirect link to the load on the system.
Now, you ask, "How do I use constant circulation with TRVs?"
MAJOR RULE!!! No matter what you do, it is possible for all or nearly all of the TRVs to be fully closed while circulation is being provided. Resistance to flow (head) will rise greatly and the circulator won't be happy. At best, its life will be shortened considerably. The solution is a simple device called a differential-pressure bypass valve. This is a three-way diverting-type valve, installed after the circulator driving the circuit containing the TRVs. The diversion path bypasses the emitters and the water heads straight back to the circulator. In normal operation, there is no diversion. If flow drops enough and head rises enough it begins to open and shortcut the water back to the circulator. As with the TRVs themselves, this is a proportional-flow operation. It will divert whatever amount of flow it requires to maintain the maximum head loss (differential pressure) setting. If you've used a TRV on every emitter in a circuit, it MUST have a differential pressure bypass valve!
How do you control the boiler and the circulator?
One fairly common method was mentioned by Mark Eatherton (above). You leave one emitter without a TRV (preferably in a space that's relatively under-radiated – often an area with high-loss, lots of windows, etc., and not subject to much solar gain). Install a wall thermostat in that room and connect that thermostat to the boiler or boiler controller. Personally, I find this method crude. It doesn't allow for true constant circulation of heated water. For instance, whenever that room is satisfied, the burner and/or circulator stop. It eliminates (or at least reduces) the "indirect" control of the TRVs, both to the boiler, and among themselves, and consequentially makes it difficult to achieve room temperature setback by way of supply temperature starvation.
If a wall thermostat must be used, my preference is to use TRVs on ALL emitters and mount the thermostat in an internal hallway that does not have a radiator. If no such space is available, try for a relatively under-radiated room but with a TRV on its emitter. For "normal" operation, such thermostat will be set somewhat higher than the desired room temperature. This provides the constant call for heat that ensures constant circulation of heated water.
If no wall thermostat is used (and your boiler isn't a Viessmann Vitodens), how do you tell the boiler to heat? Simple! Jump the T-T (thermostat) connections!
Why isn't this required with a Vitodens? Because there are no thermostat connections! And yes, you CAN do this with any boiler including mod-cons. You MUST, however, COMPLETELY disable any "boost" function because the LAST thing you want to happen is for the boiler to keep raising the supply temperature as the heat call continues. You are making a continuous heat call any time the structure requires heat. That's your objective!
In the three cases above, "control radiator", "master thermostat" or "jumped T-T," I advise you to set up the system for warm-weather shutdown. Just use a simple remote-reading setpoint controller, with the sensor OUTDOORS, and use its dry contacts to shut down the entire system when the outside temperature rises above some point. Believe it or not, 55-degrees F is frequently a good choice for the shutdown point. In the "control radiator" or "master thermostat" scheme, simply put it in series with the wall thermostat. In the "T-T jumped" scheme it merely replaces the thermostat.
So how do you control the temperature of this heated water that's constantly circulating anytime the structure requires heat?
With a conventional boiler you can technically use only the aquastat. This is NOT, however, advisable because flow through the system will vary in direct proportion to the load on the system. In mild weather, system flow will be VERY low. The TRVs will be barely open--velocity through their orifice will be high and you'll get excessive wear and noises.
MUCH better to use outdoor reset. As the outside temperature rises, the supply temperature setpoint drops. With a conventional boiler you MUST, however, be aware of the potential for damage via condensation of the flue gasses. While old original gravity systems are essentially immune, more modern systems are not! An ESBE type TV thermostatic bypass valve [likely] offers the best (inexpensive, simple, reliable) protection.
If gas is your fuel, hopefully you've used a condensing boiler (the lower the temps the better) and modulating controls (vary the fire to the load). This is where a fully TRV-ed, constantly circulating system will truly shine. It's also where you get to take best advantage of the indirect control ability of TRVs.
With a mod-con, I'd suggest TRVs on all emitters. Connect your warm-weather shutdown control to the T-T connections, perhaps in series with your "master" thermostat. The warm-weather shutdown control should also disable the secondary (emitter) circulator if primary/secondary piping is used. If you're using a Vitodens by Viessmann, there are no T-T connections; if a GB by Buderus, use the RC-10 controller as this is the type of system it's designed for.
With a mod-con driving a fully TRV-ed system, there is a term you should know. "Heat Authority"
"Heat Authority" has EVERYTHING to do with TRVs as it describes the amount of constantly circulating heat available. "Heat Authority" is also HIGHLY related to both efficiency and adjustability.
A heat authority value of 1.0 means that the temperature (thus, energy) is exactly equal to the temperature required for all of the TRVs to maintain their setpoint. Higher than 1 means that the temp is higher than needed; less than 1 means that it's less than needed.
With a mod-con, a heat authority of 1.0 is by definition the most efficient possible. However it would make it impossible to raise space temperature. After all, it's JUST adequate! In reality, heat authority is typically above 1.0. How much higher is a matter of preference and lifestyle. To get greater heat authority with a mod-con all you need do is increase the reset curve. The greater the heat authority, the faster you'll be able to raise space temperature, but there will be some "hit" with regards to efficiency. Provided the occupant has access to the curve, he or she is in COMPLETE control of both efficiency and "speed" and able to balance the two for their lifestyle.
Leave a comment
Related Posts
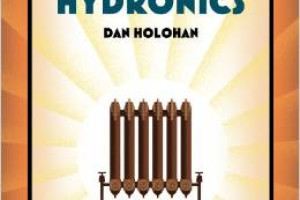
In this all-technical three-hour seminar, Dan Holohan will give you a Liberal Arts education in those Classic Hydronics systems. He’ll have you seeing inside the pipes as...
We always have turkey for Thanksgiving. I mean who doesn’t? My job wasn’t to cook it, though; it was to eat it.