This all-technical, three-hour seminar will make you familiar with the many types of old steam heating systems and what goes wrong with them. Dan Holohan’s easy-to-follow...
How Frank and John Taught Me To See
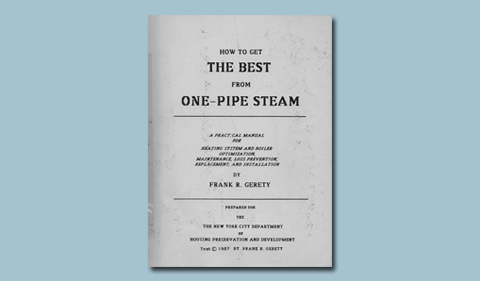
In 1989, when I was thinking about writing a book called, “The Lost Art of Steam Heating,” I went to see a young engineer named Frank Gerety. He had written a small book called, “How to Get the Best from One-Pipe Steam” for his client, the City of New York Department of Housing Preservation and Development. When it first came out, it changed just about everything.
Frank was a student of heating history and a very innovative engineer. He opened my eyes to many things. He was the first person to make me see why raising steam pressure only slows the steam on its way to the radiators. He also told me about a concept called master venting, which few heating professionals were considering at the time. That, and making dry steam, were the focus of his book.
Frank believed if you could make the steam very dry by using proper near-boiler piping techniques, you could get the steam to go further without condensing. He also believed if you vented not just the ends of the steam mains, but also the tops of the steam risers, things would work even better. He sized radiator vents based on the amount of air inside a radiator, not by that radiator’s location within a building. By doing all of this, he was following the fine example left to us by John Mills, the 19th century heating engineer who invented the Mills Boiler for H.B. Smith, and the Mills System of steam piping.
The Mills System fed steam to the top of the building through an “express” riser and then down to the radiators through a network of pipes. Mills got the steam and the condensate all going in the same direction, which solved the velocity problem most one-pipe steam systems were facing. If the steam and condensate flow in the same direction, we won’t have a problem with the steam’s high velocity holding water up in the system. It worked as promised.
One of the keys to the Mills System was that Mr. Mills vented the base of those down-feed risers. The result was remarkable. Steam traveled at about 60 mph throughout all the mains and down-feed risers and reached every radiator at about the same time. Then, all the radiator vents had to do was vent the air in the radiators. The system was balanced and the occupants were happy.
Frank Gerety, faced with existing New York City one-pipe steam systems that mostly fed up from the basement rather than down from the attic, came up with the idea of installing a main vent at the top of each riser. He piped them in place of the hand valve on the top-floor radiators. He did this by moving those radiators over a few inches and replacing the angle supply valve with a gate valve. In place of the old supply valve, he used a tee, and in the run of each of these tees, he placed a main vent dedicated to each riser.
Frank measured the cubic air volume of typical New York City steam piping systems and came up with the proper air vents for the radiators and the tops of these risers (some of which extended 12 floors). Frank’s “master venting” approach distributed steam throughout large buildings in a matter of minutes, with less than 1 psi steam pressure at the boiler. He learned how to do this by reading old books and magazines.
In the 1930s when steam was king, John Schulz also knew that this top-of-the-riser approach worked. He often vented the inlet side of those oversized radiators, which was a variation of what Frank did years later.
During the 1930s when John Schultz was working, many steam systems were switching from coal to fuel oil. The challenge was coal burns for hours and hours, making a slight pressure all the while. With this near-constant pressure, the steam was always pushing at the air, nudging it from the main vents and the radiator vents. The only time the pressure dropped was when the coal fire died down.
Because of this, the Dead Men ran their steam mains around the perimeter of the basement, running risers to the radiators off that belt of main piping. They drained the condensate though the same pipes. The main touched every corner of the basement, and all was well with the world because coal burns for a long time.
But when the 1930s arrived, the price of coal soared. Oil was much cheaper at the time, and that looked like a fine alternative. People had grown tired of coal. It was heavy and dirty and called for back-breaking work. Oil was cheap and automatic. You didn’t have to shovel the oil or clean out its ashes. There were no ashes. You didn’t need a finicky damper regulator to control the fire. And compared to coal, fuel oil was immaculate. That really appealed to the housewives, who, for the most part, were the ones responsible for building the fire each day. The best part was an oil fire worked with a thermostat, which was an amazing invention. People lined up to make the switch to oil, and coal became a memory.
That’s when John Schultz and his colleagues started having problems. Those long steam mains that touched every corner of the basement didn’t work well with an oil burner. The thermostat was somewhere in the middle of the building, and it shut off the burner before most of the air was out of the steam mains. The building would be warm on one side and cold on the other.
The oil dealers solved the problem by piping the new buildings with multiple horizontal steam mains, balancing one against the other. This was when we began to see headers on steam boilers with multiple takeoffs for the mains. Watch for this, and for those perimeter mains, when you’re roaming basements. It will give you a good sense of the system’s age, and whether or not the Dead Men originally piped it for coal or for an automatic fuel such as oil or natural gas.
On the older jobs (those that were piped for coal) the oil men solved the balance problem by using very large main vents. They were taking a page from John Mills’ book. They knew if they could vent the main very quickly, the steam would favor that route before it rose up the risers. The mains became the path of least resistance to the steam. John Schultz and the others would be able to fill the horizontal main like a trough, because that was the easiest path for the steam. By using those large main vents, the Dead Men coaxed the steam into arriving at all the risers that led to all the radiators at about the same time.
When Frank Gerety began doing his work in New York City during the 1980s, he was writing mainly about the problems caused by wet steam. He was coming up with innovative ways to pipe steam boilers to dry the steam, and his focus was on apartment buildings of all sizes.
Frank also realized that trapped air was a big problem in buildings of this type. He knew that steam wants to move at 60 mph, and the only thing standing in its way was air. So he looked back to the approach John Schultz and the others had taken 50 years earlier, and he revived the concept of master venting. I watched his work as it evolved, and it amazed me. In the master vented buildings, the steam traveled faster than I could run. These systems went into balance with just ounces of pressure at the boiler, and the burners didn’t short-cycle.
This was when we all began to see the low-hanging fruit. We actually could make steam work well and economically.
The challenge, though, was the air-vent manufacturers were telling people to vent by geography, not by air volume. They said radiators closest to the boiler should have slower air vents than radiators that are furthest from the boiler. The more Frank thought about this, the less sense it made to him. And looking back, John Schultz had said the same thing all those years ago.
It comes down to this: Big rooms have large radiators because they have a large need for heat. Small rooms have small radiators because they have less need for heat. On the coldest days, we want both the large and the small radiators to heat from one end to the other, and we want that to happen at the same time. If it can do that, the system will be in balance.
It really doesn’t matter where the radiator is within the building. What matters is system balance. All the radiators should heat fully on the coldest days of the year. It’s as simple as that. It’s not about radiator location; it’s about the amount of air to be vented from each section of the system. It’s about master venting.
John Schultz was gone long before I was born. Frank Gerety passed on March 30, 2015, much too soon. They were great men, and they both taught me to see.
Rest in peace, gentlemen. Your work lives on.
Leave a comment
Related Posts
We always have turkey for Thanksgiving. I mean who doesn’t? My job wasn’t to cook it, though; it was to eat it.
I had written a story for Plumbing & Mechanical a while back about a fella in Canada who sent me this email: "Our problem is that five out of hundreds of univentilator co...