This all-technical, three-hour seminar will make you familiar with the many types of old steam heating systems and what goes wrong with them. Dan Holohan’s easy-to-follow...
How to Replace an Old Steam-Heating Boiler
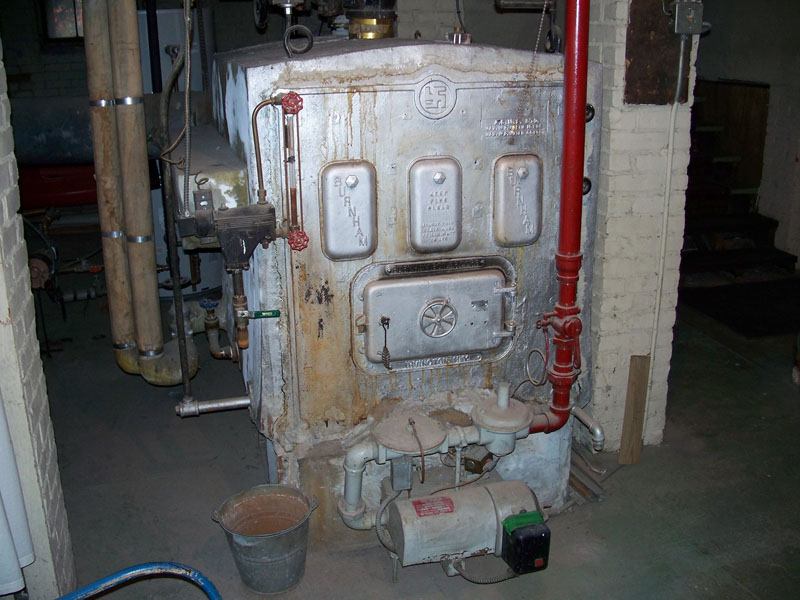
Here are some good tips for you.
Base the size of the replacement boiler on the connected load, not the building’s heat loss. The boiler’s ability to produce steam must match the system’s ability to condense steam. It really doesn’t matter what the building’s heat loss is. The radiators and pipes are going to condense steam at a certain rate, and if the boiler is too small (which usually happens if you size it based on the heat loss), the steam will go just so far. You’ll wind up with a building that has either hot rooms or cold rooms, and there’s not much you can do to cure the problem at that point.
Go from room to room and survey the radiators. Then use a suitable pick-up factor for the piping. If you look in a boiler manufacturer’s catalog you’ll see they’ve already built in a pick-up factor. It’s the difference between the Net load and the D.O.E Heating Capacity load. It’s standard to increase the Net load by a factor of 1.33 nowadays to get to the Heating Capacity. If you notice that radiation is missing from the building, though, or if you see there’s no insulation on the pipes, the piping pick-up may be more than you expect. In cases such as these, protect yourself by using a larger pick-up factor. Measure the radiation and multiply it by a factor of 1.5. Then select the boiler from the D.O.E. Heating Capacity column, not the Net column. You’ll be glad you did this when that boiler starts for the first time.
If you find the building is over-radiated, consider removing radiators, or better yet, use thermostatic radiator valves at the existing radiators. Don’t downsize the boiler figuring each radiator will get "half-hot." What will actually happen is that a portion of the radiators in the building will get fully hot while the others stay stone cold.
If the boiler goes back to the Coal Era, know that it may be 75 percent larger than it has to be. It was standard to increase the boiler by that much in the old days because engineers weren’t certain the owners could make proper coal fires. By oversizing, they pretty much guaranteed there would be enough heat – even with lousy firemen. A contractor friend regularly measures the radiation and comes up with steam boilers of, say, 60 horsepower where 100-horsepower boilers are already on the jobs. The smaller boilers work beautifully. Never base the size of a replacement steam boiler on the old boiler’s rating. Survey those radiators. It’s the only way to be certain.
Be aware of water levels. This is more important in gravity-return systems than it is in pumped-return systems. If the new boiler’s water level is too high, there may not be enough vertical space between the boiler water line and the end of the steam main (in one-pipe systems), or the lowest steam trap (in two-pipe, gravity-return systems). The result? Returning condensate backs up into the mains causing water hammer. This usually happens in the middle of the steaming cycle.
If the water level of the new boiler is too low, there’s a chance you may turn what was a wet return (a pipe below the boiler water line on a gravity-return system) into a dry return (a pipe that’s above the boiler water line). Here again, your reward for making this mistake is water hammer. If you find an old boiler that’s sitting up on a pedestal, know that it’s there to cover a return line on the building’s first floor. This was once a very common piping practice in apartment buildings. If you install your new boiler off the pedestal you’ll have to create a false water line to avoid water hammer. My book The Lost Art of Steam Heating goes into detail on how to make one of these wonderful devices. You can get a copy in the store.
Check out the replacement boiler’s steaming capabilities. There are several things that make for a good steam boiler. First, if it’s a cast-iron boiler, the interior width of the sections should be as broad as possible. If it’s a steel fire-tube boiler, there should be plenty of space between the tubes. When water turns to steam inside a boiler the steam forms at the point of greatest heat. This is down there at the bottom of the boiler where the static pressure is also the greatest. As the steam bubbles break free from the metal and rise to the surface of the water, each bubble increases in size. If there’s not enough space for this to happen, the bubbles will crowd each other and create surging. If the sections are very narrow, or the if tubes too close together, the water inside the boiler will fill with steam and become less dense than the water in the gauge glass or the pump controller’s water column. When the burner shuts off, the steam bubbles will suddenly condense. That can drop the water level in the boiler to a point lower than the level in the gauge glass or water column. The water level in the glass or column will then fall into the boiler. That makes the boiler-feed pump short-cycle and the low-water cutoff bounce on and off. Choose a boiler with lots of internal space.
Look, too, for a boiler that has as much vertical space as possible between the center of the gauge glass and the steam outlet. Boilers with top outlets generally produce drier steam than boilers with side outlets. You want that outlet to be as far away as possible from the surface of the water to avoid carry-over. A sectional cast-iron boiler is less susceptible to changes in boiler water level than a steel, horizontal-fire-tube boiler because of the difference in shape. When the water rises a few inches in a round, horizontal boiler, the steaming space gets smaller because the water is reaching the top of a circle. In a cast-iron, sectional boiler, this doesn’t happen because the water is rising to the top of a rectangle rather than a circle.
Compare the exit velocities of several boilers before you settle for one. The formula for figuring steam velocity is:
Steam Velocity = Lbs./Hr X Cubic Volume of Steam (at the system’s pressure)
25 X Internal area of the steam nozzle
Base the Lbs./Hr per hour on the Heating Capacity of the boiler. The rest you can get from a steam table and a good piping handbook. The lower the velocity, the drier the steam, and the better the steam boiler. Choose a boiler with the lowest possible exit velocity.
Check the steaming rate of the boiler against the time lag of the system. A replacement steam boiler will usually hold less water than the old boiler. Because of this, you may not be able to use that new boiler on a gravity-return system without adding a boiler feed pump (and a false water line). If the job has a condensate pump, you may have to switch over to a boiler feed pump. The only way to know for sure is to find out how much water is in the operating range of the replacement boiler. That’s the vertical space between the center of the gauge glass and the low-water cutoff point. You’ll probably have to ask the boiler manufacturer for this information since few publish it. Once you get it, know that all boilers, regardless of size or type, steam at a constant rate of ½ gpm/1,000 sq. ft. EDR (one sq. ft. EDR equals 240 BTUH in steam heating work). Now that you know how much water is in the operating range of that new boiler, and since you know its D.O.E. Heating Capacity, you can figure out how long it will run before it shuts down on low water.
Next, time the lag between steaming and return. Run the old boiler and begin timing when the header gets hot. Find how long it takes for the steam to work its way around the system and return as condensate. In a gravity-return system, feel the end of the furthest main and stop timing when it gets hot. In a system with a condensate pump, you’ll stop timing when the pump starts for the first time. Be aware that clogged returns, missing air vents, and poorly pitched pipes can affect a system’s time lag.
If you don’t have enough water in the boiler’s operating range to satisfy the system time lag, you’ll need a boiler feed pump (and a false water line). If the old boiler isn’t operating, you won’t be able to time the lag. At that point, you’ll be making an educated guess, and this is where steam heating crosses the line between science and art, which is why I called my book The Lost Art of Steam Heating. Get yourself a copy from our store!
Use the boiler manufacturer’s near-boiler piping diagrams. Nowadays, you have to consider near-boiler piping to be a part of the boiler because manufacturers depend on it to act as a separator for carry-over water. Check out the directions in their installation manuals and follow them exactly. Also, read what the manufacturer has to say about cleaning the boiler and the system and follow that as well. And if you need more help, come back here.
Leave a comment
Related Posts
We always have turkey for Thanksgiving. I mean who doesn’t? My job wasn’t to cook it, though; it was to eat it.
I had written a story for Plumbing & Mechanical a while back about a fella in Canada who sent me this email: "Our problem is that five out of hundreds of univentilator co...