In this presentation, Gary Klein shares important information about air source heat pump water heaters (HPWH), with particular attention paid to where the warm air comes ...
Pumping Away Piping
This is an excerpt from Dan Holohan’s book Pumping Away and other really cool piping options for hydronic systems.
Since you've read this far, I figure you must be pretty open-minded. You may even be willing to break a few old habits - if it's to your advantage, I mean. I wouldn't want you to do it for any other reason. There's gotta be something in it for you.
And that's why I'd like you to give this piping arrangement some consideration. There's a lot in it for you.
You leave the boiler with a full-size supply main and enter a tee. Pipe a 1/2" boiler drain into the top of the tee. That's going to be the purge valve for your system. You only need one purge valve. You take the money you were going to spend on the other purge valves and you go buy something nice for yourself.
Now, come off the side of the tee, keeping the pipe full size as you go, and install either a ball valve or a gate valve. You'll be using this valve for service, as well as for your initial air purge.
Your air separator comes next. If you're using a scoop- or orifice-type air separator, you'll need to allow 18 inches of straight, full-size horizontal pipe at the inlet to the air separator. The manufacturers of these types of air separators call for this approach piping. They need it to get the maximum efficiency out of their units. If you're using a microbubble reabsorber-type of air separator, you won't need this approach piping; you can install this type of air separator right next to the ball or gate valve.
Okay, next we have the compression tank. You'll attach it to, or very near the air separator. In this example, I'm using a diaphragm-type tank. I'll show you how to use a plain-steel tank in a minute.
Bring your feed valve into the line connecting the diaphragm tank to the system piping. That's the point of no pressure change, the only place in the system where the pump can't affect the feed valve. You'll be using the feed valve, the main service valve and the tee-mounted boiler drain to power purge the air from the system. You push it all in one direction.
That's one of the best things about this piping arrangement. It lets you power purge toward the system piping and up through the bottom of the boiler. You can power purge one zone at a time and never wind up with a big bubble of air trapped inside the boiler. This, whether you realize it or not, often happens when you pipe your feed valve into the boiler and your purge valves on the return. You need that one main shut-off valve to get everything going in the same direction.
Okay, next come your circulators. Here, I'm using two, but you can have as many as you'd like. After each circulator, you'll pipe in a flow-control valve to prevent gravity circulation and short-circuiting, and then a ball or gate valve for service and the initial power purge.
If you prefer to zone with valves instead of circulators, pipe the job like this.
In either case, you'll get rid of your initial air by closing the main service valve and the zone service valves. Next, open the feed valve and the tee-mounted boiler drain. Then, open one zone at a time. It's like firing torpedoes.
The water will flow through the first zone, pushing air ahead of itself. The air will zip through the boiler and leave the system by way of the tee-mounted boiler drain. The water will also fill the boiler.
When the water runs air-free, close that zone's service valve and open the next zone's service valve. Bam! The water will push the air through the second zone and the already-filled boiler.
If you have a dozen zones, do this a dozen times. You only need that one power purge valve, and you won't wind up with that big bubble in the boiler.
When you start the system, the pumps will add their differential pressure to the system's static fill pressure and move whatever air comes out of the heated water back to the air separator.
In most cases, you'll find you don't have to go upstairs to bleed the radiators. You'll be doing it all from the basement - even on diverter-tee systems! The system will run quietly, with no pinging or waterfall sounds. You've put the combined forces of Boyle's Law and Henry's Law and Mother Nature on your side.
You may never have to bleed a radiator again.
One guy took me up on this challenge a few years ago. He tried it on a diverter-tee system and then he called me at home.
"Dan," he said, "I have never run across a diverter-tee system that didn't make me crazy. It usually takes me over an hour to get rid of the air, and that's what I thought would happen here, but I was willing to give it a shot because I figured you had nothing to gain by lying to me."
"That's right," I admitted. "Whether you put the pump on the supply or the return, it doesn't put a nickel in my pocket. I only tell you these things because they're true."
"Well," he continued, "I started the pump and went out to my truck to get a can and a rag and a screwdriver. Not that I doubted you or anything. I just figured you might be full of bull so I might as well get ready."
"And what happened?" I asked.
"Well, when I got to the first convector, it was already hot!"
"How about that!" I said.
"And every other was hot as well," he explained. "I've never seen anything like this!"
"That's what happens when you work with your head as well as your hands," I told him. "You have Mother Nature and Mr. Boyle and Mr. Henry on your side now."
"You know, you're not as dumb as you look," he said.
"I couldn't possibly be."
Want to read more? Check out Dan Holohan’s book Pumping Away and other really cool piping options for hydronic systems.
Leave a comment
Related Posts
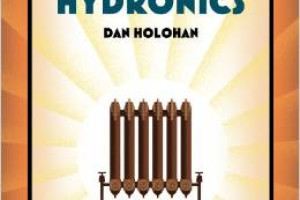
In this all-technical three-hour seminar, Dan Holohan will give you a Liberal Arts education in those Classic Hydronics systems. He’ll have you seeing inside the pipes as...
We always have turkey for Thanksgiving. I mean who doesn’t? My job wasn’t to cook it, though; it was to eat it.