This all-technical, three-hour seminar will make you familiar with the many types of old steam heating systems and what goes wrong with them. Dan Holohan’s easy-to-follow...
The Importance of Air Venting in Steam Systems
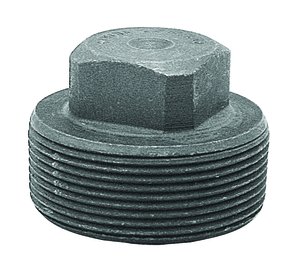
Years ago, in some dank basement, a contractor installed a large air vent near the end of a steam main. He did this because he knew that steam and air are both gases, but steam is lighter than air, so the two won’t mix. He also knew that the empty steam main was going to start out filled with air (which is only natural, right?), and that once it left the boiler, the steam would shove the air ahead of itself and down the main, just like a big, hot plunger. The contractor sized the air vent to release the air from the pipe at a certain rate so that the steam could move faster than he could run. The design velocity for steam in a space-heating system can be as high as 60 miles per hour. The only thing standing in the steam’s way is air.
The contractor piped that vent and started the system, and it worked just as planned. But he wasn’t surprised; he did this work every day, and he knew his business. He knew how to “think” like steam and like air. He knew that the air wanted a way out of the pipe, and that the steam was more than willing to give it a shove. That’s why the air vent near the end of the main was so important, and why the contractor had to size it properly.
Time went by and the contractor eventually became a Dead Man. For many years, the steam plunged that air toward that vent, and the air left the system exactly as planned. The steam gave up its latent heat to the radiators and condensed into water, shrinking to 1/1,700th the size it had occupied as steam. That’s the expansion ratio between water and steam: 1,700:1. Think of it; one glass of water becomes 1,700 glasses of steam. And vice versa.
As the steam shrank back into water, a vacuum tried to form inside the steam main, but Mother Nature abhors a vacuum, and by this point, that big air vent had reopened, allowing the air back into the steam main. Every steam heating system ever built does this. It breathes out and it breathes in, just as we do.
When the air returned, the inside of the pipes was dripping wet from the steam. The oxygen in the air reacted with the wet metal, causing it to rust over time. Every steam heating system ever built rusts from the inside because every steam system ever built is open to the atmosphere.
The steam kept coming and coming and it moved so quickly that it carried with it the particles of rust and other solids that made its way into the system with the fresh feed water. Much of that crap wound up inside that big main air vent. It got stuck between the pin that closes the vent and the hole that releases the air from the vent. That’s when the vent started to leak steam and water. It began slowly and no one noticed at first, but then it got worse and someone called in a new contractor.
This contractor hadn’t grown up installing steam systems because people were now using hot-water systems in new buildings. The steam business had become one of replacing boilers and fixing parts. The new contractor had never seen an air vent like this one, so he removed it and took it down to his local supply house. He showed it to the counterman, who also had never seen one like this one.
“What’s the problem?” the counterman asked.
“It’s squirting steam and water all over the place,” the contractor said.
“I know how to fix that!” the counterman said, and he handled the contractor a ¾” pipe plug.
“I’ve got these on the truck,” the contractor said.
“So go use it,” the counterman replied, and that’s what the contractor did.
It is now time to think like steam.
Back on the job, the steam was still trying to push the air from the vent, just as it had been doing for so many years. But now the vent was gone and there was a plug in its place. Plugs do a very poor job of venting (hence their name), so the air just collected down there near the end of the main, like traffic on a closed road. But the steam was flying out of the boiler. It didn’t know the road was now closed. It was just trying to go to work as usual. It kept pushing and pushing, and pretty soon, the air had enough. It turned around and pushed back. Gases will do that. Try to compress them and the pressure will build. We call this Boyles Law.
The people in the building weren’t happy because a good part of the building was now cold. This is because where there is air, steam will not go.
So they called the contractor.
The contractor returned and felt the steam pipe. It was piping hot up to the point where the steam could reach, but a foot or so down the line, it was cool to the touch. This was because that part of the pipe contained nothing but air, and where there is air, steam will not go (are you getting this?).
“The pipe must be clogged,” the contractor muttered to himself; and it was clogged, but with air, and few people think about air because they can’t see it.
“Let me raise the steam pressure and see if I can blow this clog free,” the contractor muttered. He went to the boiler room and adjusted the device that controls the pressure (we call this a “pressuretrol”), raising it from two-psi pressure to five-psi pressure. Then he waited 10 minutes or so.
To his delight, the steam had moved further down the line! This was because of Boyles Law, and also because of the First Law of Steam Heating, which states, When you do something stupid, you will always get a reward, which leads you to do things of even greater stupidity. By raising the steam pressure, the contractor had allowed the steam to further compress the trapped air. The air still had nowhere to go because that ¾” pipe plug was still doing what its name implies, but from the contractors’ point of view, it looked like progress.
“Let me raise it a bit more,” he mumbled.
Now he had the pressure up to eight-psi and the boiler ran almost all the time, burning lots of fuel as it did. The air was jammed up against that pipe plug and the steam reached further into the main, but never got to the end. He told the customer that this was the best they could expect. “It’s steam,” he said. “It’s old.”
The customer nodded and let it go at that. The following month, when the customer received his fuel bill, he gagged. It had never been this high. And that’s a shame because you can move with a pinhole what you can’t move with a ton of pressure. A simple main vent, properly sized, would have solved this problem and lowered that fuel bill.
Steam is like a delivery van. It moves down the road quickly, and it carries a full load of heat in its cargo bay. But if the road is closed, the van will just sit in traffic along with the rest of the cars and trucks, and the heat will never get to the customers who are anxiously awaiting delivery. And they’ve already paid for it.
If you “think” like steam and like air, you’ll be able to see this, and you’ll be able to do things others say can’t be done. That’s how you build a reputation. And once you do that, you will have very few competitors.
Trust me on that.
Leave a comment
Related Posts
We always have turkey for Thanksgiving. I mean who doesn’t? My job wasn’t to cook it, though; it was to eat it.
I had written a story for Plumbing & Mechanical a while back about a fella in Canada who sent me this email: "Our problem is that five out of hundreds of univentilator co...