This all-technical, three-hour seminar will make you familiar with the many types of old steam heating systems and what goes wrong with them. Dan Holohan’s easy-to-follow...
The Importance of Near-Boiler Piping in a Steam System
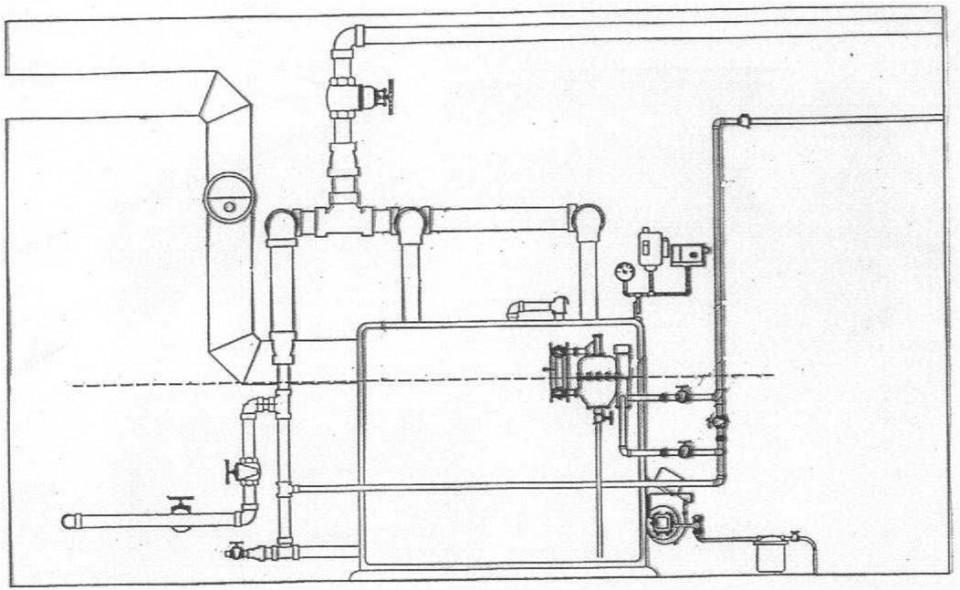
Years ago, steam heating was a business of installing complete systems and not just a business of replacing boilers and fixing problems, as it is today. Manufacturers made boilers that could produce dry steam, which means that no more than two percent liquid water left the boiler with the steam. Those boilers were able to send that ferocious dry gas through pipes at 60 miles per hour and they did this by separating the water from the steam internally.
All that changed in the ’80s when the boilers got smaller. They had to get smaller so they could meet the call for higher combustion efficiency. The internal sections got narrower and the steam now had to climb through a tighter space. That led to more violent waterlines and wetter steam. The steam-disengaging space also got smaller and that made things worse. Oh, and the exit holes in the boilers shrank, which led to exit velocities that had the steam pulling the water out of the boiler and into the system. That gave us uneven heat, high fuel bills, and quite often, water hammer.
Weil-McLain, to their credit, drags a big steam boiler to the tradeshows in the East. They cut a porthole in this boiler so folks can see what goes on inside. And they piped the boiler perfectly with glass pipe because seeing is believing, and this boiler is there to make people believe.
When they fire this beast you can see the steam forming within a few minutes. As it races from the boiler, it pulls water with it. They used two risers from this boiler and offset the tops of those risers with elbows before connecting to the header. In a real boiler room, that piping would be steel and threaded so the header can move against those elbows as it expands and contracts. This keeps stress off of the boiler sections. It’s the reason why copper is a bad idea when it comes to steam piping. The twisting can break a soldered fitting.
But about those two risers. They use two instead of one because two risers cut the exit velocity of the steam in half. The slower the steam goes, the less boiler water it will take with it. If I was piping a steam boiler and it had 10 holes for risers, I’d use them all. Dry steam can heat a building. Wet steam just wastes fuel, leads to water hammer, and makes everyone miserable.
So you stand there at the tradeshow and watch this wonderful, glass-piped boiler. Within a few minutes, boiler water has completely filled the two risers to the header and is spilling over into the header. People stare in amazement. The person running the show explains that this is normal. It is the nature of a modern steam boiler for space heating.
The now-full risers reach up about two feet above the top of the boiler before turning to connect with the header. If they were shorter, the carryover water would fill the header and you would be looking not at a steam boiler, but at a hot-water boiler. It’s tough to heat a steam system with a hot-water boiler.
I’ve been looking at steam systems since 1970. I’ve read many books about them, and written a few myself. I notice nowadays that some boiler manufacturers are calling for the header to be a minimum of 24 inches above the boiler’s waterline. I don’t think that’s enough, and I think the Weil-McLain glass-piped boiler proves that it’s not enough. I think the bottom of the steam header should be a minimum of 24 inches above the top of the boiler jacket, and more than that, if possible. The higher the header, the drier the steam will be.
Pros who do steam know this. Many of them use a Dead Man trick called a drop header. This is where you bring your risers to a very high point, and then turn with your elbows first over and then down before entering your header from the top. You can learn more about drop-header piping HERE.
I wish the boiler people would get together and take another look at that dimension. It should be two feet at least above the top of the boiler, not above the waterline. It’s a fine point, but a very important one, and everyone will be better off if they made this change.
In the meantime, I hope you’ll make the change for yourself. You’ll have fewer headaches if you do.
So much for the pipes. Now for the valves:
When you quote that next steam boiler-replacement job, suggest a king valve and a return valve to your client. A king valve goes on the pipe that leads from the header to the steam main. You’ll need more than one if you have more than one steam main leaving the header. The return valve goes (you guessed it) on the wet return, just before it meets the Hartford Loop. You’ll also put a full-port ball valve in the boiler’s mud leg.
You like that name? Mud leg? I do too. I like it because it describes perfectly what goes on in the bottom of a steam boiler that serves an old steam system. Here we have pipes, valves, fitting and radiators that are perhaps 100 years old. Every steam-heating system is open to the atmosphere. When you wet iron and steel and then expose it to the air you get rust. And when you let steam, moving at 60 mph, through those pipes, all that rust gets shoved down the line and winds up at the low point in the system, which is the boiler’s mud leg. Let enough mud accumulate and you’ll lose the circulation though the boiler. Lose the circulation and you lose the boiler.
So there you are with the client. You’re there because the old boiler isn’t working anymore. Maybe it failed because of mud. So you suggest the king valve, the return valve and the full-port ball valve on the mud leg. You explain that you’ll come back each year to close the king valve and the return valve. That will allow you to isolate the boiler from the system and build about 10-psi pressure inside of it. You can’t do that without the king valve and the return valve. You’ll explain that once you have that 10-psi pressure, you’ll open that big full-port ball valve on the mud leg and blow out a year’s worth of crap. The extra expense of those three valves now will add decades to the life of this boiler.
Your competitor may tell your client that these valves are a waste of money. He’ll say that he can clean the boiler without them. But consider this: A column of water 28-inches high exerts only 1-psi pressure at its base. How high a column can you raise inside that steam boiler? Even if you flood the boiler, you’re probably not going to have more than about two-psi of static weight.
Think you can flush thick, sloppy mud, mud made of heavy iron and steel particles, with just two-psi of static pressure? I don’t think so either. And keep in mind that as the level goes down while that knucklehead is draining the boiler, so does the static pressure. Sure, the water will flow from the boiler, and the knucklehead will think he’s doing great things. But the mud crouch inside the boiler and laugh at him.
Suggest those extra valves. The money the client spends with you now will bring lots of dividends in the years to come.
I told this story to a contractor I met at a tradeshow and he said to me, “Do you know what those valves cost? Those are big valves! My customers won’t go for them?”
“Are the valves more expensive than a boiler?” I asked.
“No, but they won’t go for them,” he said.
“Have you explained what I just explained and asked the client? How can you be sure if you don’t explain and ask.”
“They won’t go for it,” he said.
So there you have it. Think you can compete with that guy?
Leave a comment
Related Posts
We always have turkey for Thanksgiving. I mean who doesn’t? My job wasn’t to cook it, though; it was to eat it.
I had written a story for Plumbing & Mechanical a while back about a fella in Canada who sent me this email: "Our problem is that five out of hundreds of univentilator co...