In this presentation, Gary Klein shares important information about air source heat pump water heaters (HPWH), with particular attention paid to where the warm air comes ...
Types of PEX pipe
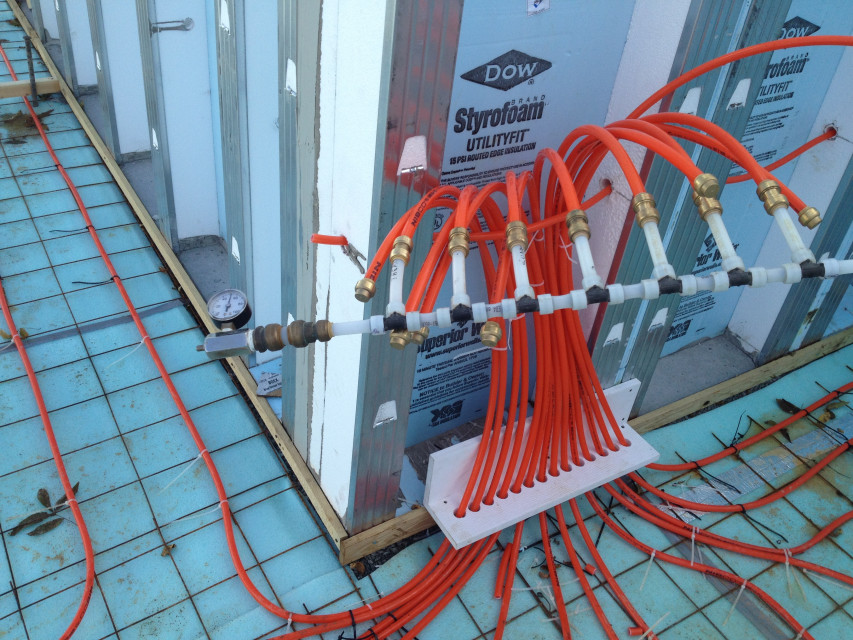
You have options when it comes to the tubing you bury or staple up on a radiant job. You may choose to go with a particular supplier and never question the type of tubing they provide. That's a legitimate choice, if you trust the suppler.
Nowadays, most suppliers deal with some sort of PEX tubing. PEX is an acronym for polyethylene, crosslinked. It's very good stuff from what I've seen. It's also made to last about 200 years, but you and I will never know for sure if that's true because we will both have joined the ranks of the Dead Men by then. PEX is, however, the material you’ll find all over Europe. The Europeans have been doing hydronic radiant heating with PEX since the early Seventies and there's a lot more of it there than there is here. PEX has a great track record and has reached the point where it’s almost considered a commodity item by many heating contractors and plumbers.
To avoid having it become a commodity (which is the kiss of death for any manufacturer), PEX manufacturers have been taking the time to spell out the differences between their products. And there are differences in the way different companies make PEX. Knowing this can help you make the right decision when you're shopping for a PEX supplier. Here's the deal.
Most manufacturers start with a material called HDPE, which stands for High-Density Polyethylene. HDPE evolved from polyethylene, a material discovered by accident by a group of British scientists during the 1930s. Polyethylene played a huge part in World War II because it gave the British the ability to carry radar on their airplanes for the first time in history. This was during the Battle of Britain. The German pilots didn't have radar (and they didn't know that the British did) so the British were able to kick the stuffing out of the Nazis by shooting at them from behind the clouds. But that's a story for another day.
PEX differs from HDPE in that PEX has this special three-dimensional link between the molecules. Scientists call this stuff a "macro-molecule." What that means is that if you hold a 200' coil of PEX pipe in your hands, you're actually holding only a few molecules. Pretty strange, eh? It's this network of macromolecules that gives PEX such a fine memory for its original shape. If you kink PEX pipe, you can just heat it up and it will always return to the shape in which it was first crosslinked.
The linking of the molecules happens during the manufacturing process, and how a manufacturer chooses to make that happen affects the properties of the final product. The manufacturer can't link all the molecules together because that would make the PEX too brittle. On the other hand, if they link too few molecules the material won’t be any better than HDPE, from whence it came. They have to find just the right combination of linked and non-linked molecules. There are different ways to get where they need to go, and from what I’ve learned, some ways seem better than others. Here are the principal methods manufacturers are using today to make PEX:
Engel-method PEX (also known as PEX-A) This is the stuff Tomas Engel brought into the world. Engel was the guy who invented PEX. He is a European scientist and he had nothing to do with the radiant heating industry when he invented PEX. I heard him speak at a meeting in Sweden in 1990 and was fascinated by his story. But that, too, is a story for another day. What's important for you to know is that Engel-method PEX gets crosslinked while it’s still in its melted form. The manufacturers do this by adding peroxide to the mix and then applying a tremendous amount of pressure and temperature to the liquid. What comes squirting out of the machine is PEX that's as clear as glass. As it cools, it takes on a darker color. The Engel method gives the pipe an essentially uniform distribution of the crosslinking sites throughout the material. From what I’ve read in independent scientific papers that have come from Europe, this is the best way to make PEX. It takes a while longer to do it this way, and this sort of PEX may cost a bit more.
Irradiation-method PEX (also known as PEX-C) Irradiated PEX starts out as straight polyethylene tubing. As with other methods of making straight polyethylene, the tubing takes on a definite form during the extrusion process. With the irradiation method, the crosslinking takes place in a second process when the manufacturer runs the tubing through an electron beam cannon. The beam gets the polyethylene molecules so excited that they crosslink.
This method can sometimes result in a less uniform crosslinking of the material, however, especially if the pipe is larger than 1" in diameter. This happens because the thicker pipe requires a higher dose of radiation. If it’s not done properly, the outer layer of irradiated PEX can become brittle, but this is not a concern in a well-controlled process. If the pipe maker is experienced there is no need for concern with this sort of PEX when used on a radiant heating system. Buy in the mainstream and you'll do fine.
Silane-method PEX (also known as PEX-B) The big difference between this method and the other two methods is that with the Engel and Irradiation methods, the crosslinking consists of a bond between carbon molecules. With the Silane method the crosslinking takes place across silicon and oxygen molecules. These links are weaker than the carbon-carbon links that result from the other methods, and this may have an effect on the long-term chemical stability of the material. If we live long enough, we’ll probably find out.
I hope all this chemistry isn't making your head spin. I think it's good for you to know the differences between these materials even though they all go under the name PEX. Let's face it, you're the one who’s going to be putting the tubing under the floor.
In fairness, though, I have to tell you that none of these methods is a bad method; The American Society for Testing and Materials (ASTM) approves all three methods. However, in a world among "equals," it seems to me that some methods are more "equal" than others. Don't think of PEX as a commodity item. There is a difference.
And that brings us to this last one:
PEX/Aluminum/PEX I first saw this tubing in 1991 at the big ISH fair in Frankfurt, Germany. I was walking past one of the booths in the radiant heating building when a salesman handed me what looked like a plastic cane. He didn’t pick me out of the crowd; he was giving canes to everyone who passed. I thought the kids would like it so I took it and twirled it like Charlie Chaplin as I continued down the aisle. But then it suddenly occurred to me that what I was twirling was hydronic radiant heat tubing (this stuff was so new to me in 1991). I walked back to the booth and asked about it. They found someone who could speak pretty good English and he explained that this tubing had an aluminum core that was sandwiched by two layers of PEX. "The aluminum keeps out the oxygen," the representative told me. "And when you bend it, it stays bent!" This I could see as I looked at the cane. "When you put it down on the floor, it doesn’t bounce back up at you." He gestured by flailing his arms.
When you put it down, it stays down. And that's the benefit of PEX/Aluminum/PEX. That, and the fact that it doesn’t expand as much as straight PEX. Less expansion means less noise if you're using PEX on a staple-up job.
Leave a comment
Related Posts
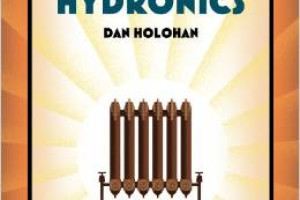
In this all-technical three-hour seminar, Dan Holohan will give you a Liberal Arts education in those Classic Hydronics systems. He’ll have you seeing inside the pipes as...
We always have turkey for Thanksgiving. I mean who doesn’t? My job wasn’t to cook it, though; it was to eat it.