This all-technical, three-hour seminar will make you familiar with the many types of old steam heating systems and what goes wrong with them. Dan Holohan’s easy-to-follow...
Where is the Water Line?
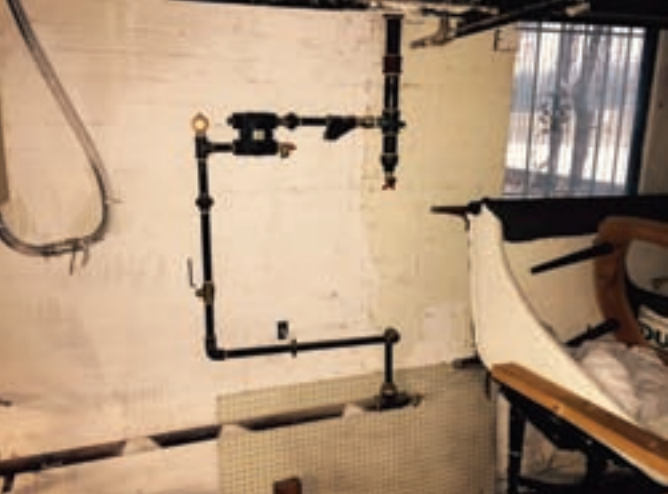
We service the steam system in an old apartment building in the Dupont Circle neighborhood of Washington, D.C. The Avondale Apartment Building was built in 1914, and has a one-pipe steam system with cast iron radiators. It features a Mills Systems piping arrangement. Two large mains are piped directly to the attic, one for each wing of the building. The mains circle the attic and drop back down to the basement along each tier of radiators. This type of piping allows the steam and condensate to flow in the same direction, heating the building quickly, quietly and evenly. That is, when everything is working well.
We first got involved with the project about 10 years ago. The boiler has recently been replaced with a Burnham V-11 cast iron sectional boiler with a power gas burner. They could not get the system to heat properly and there was severe water hammer. We were called in to see if we could solve the issues with the steam system.
When I surveyed the installation, the first thing that caught my eye was a new boiler feed pump. Boiler feed pumps can do a great job of maintaining a steady water line, especially if the new boiler does not hold as much water as the older boiler it replaced. It can store condensate and pump it into the boiler as needed, preventing the burner from shutting off on low water. A boiler feed pump can also create problems if added to a system without thoroughly checking out the piping.
In this case, each down-feed main dripped into a wet return where it was drained by gravity back to the boiler. It worked beautifully for 85 years, until the boiler freed pump was added. This opened up the wet returns to the atmosphere. Without a water seal at the base of each down-feed main, steam blew through the returns and up adjacent mains, creating horrendous water hammer. It also blew live steam through the boiler feed pump receiver and out the vent pipe.
The original contractor attempted to correct this by adding a large “master trap” at the inlet to the receiver. This never works. It only created more problems. But at this point, he was just trying to make the system work and stop hammering so he could get paid. He was desperate and grasping for a solution.
The solution would not be easy. We came in and cut in F&T traps at the base of each down-feed main (See photo). We also cut in main vents to quickly vent the air from the mains and risers. The F&T traps kept the steam out of the returns and allowed the condensate to drain back to the boiler feed pump receiver. We removed the master trap from the pump receiver. This resolved the issues, restoring even heat and peace to the building. Everyone got paid, everyone was happy.
Other than routine maintenance and repairs, all was well for almost 10 years. Then, I got the call this past December. One entire tier of radiators would not heat.
“Can you come out and check on the problem?,” the chairman of the building and grounds committee asked me.
“No problem,” I responded. “I will be there tomorrow.”
I had already solved this one as I was driving to the job site, making a cardinal mistake. Never decide what the problem is until you do a thorough survey and analysis. But, I already decided I had a clogged or failed F&T trap. But in this case, I was only partially right.
I took apart the Y-strainer before the trap and flushed it out. I went ahead a replaced the F&T trap, even though it checked out. I wasn’t taking any chances. After these repairs, the tier still would not heat.
On this cold mid-December day, the boiler was firing and all of the mains and radiators were hot. Except all of the radiators on this one tier. From the main floor, to the seventh floor, every radiator was cold. We got into an apartment on the fourth floor. Sure enough, the downfeed main and radiator were stone cold.
I fiddled with the valve, opening and closing it, but it appeared to be OK. Maybe the bullet vent failed. I unscrewed the vent and was immediately sprayed by a torrent of water under pressure.
“I think we have a hot water system, not a steam system,” the tenant suggested.
I always appreciate when the tenants offer their advice.
I was wiping off my soaked face and shirt, for the time being ignoring this huge clue in front of me. Why would there be water under pressure on the fourth floor of a steam down-feed main?
After sketching out the piping and thinking it through, the problem jumped out at me. The main was clogged at the base. Condensate was filling up the main cutting of steam to that tier of radiators. Even on the fourth floor, there was still 30 feet of static pressure above the radiator, which is why water sprayed out of the vent like a fire hose. Once the entire riser was filled with condensate, it spilled into the steam main circling the attic where the steam slammed it around like a bowling ball. This was the cause of the water hammer they were hearing.
All we had to do was find the base of the main, cut it open, and flush out the clog. Only, it is never this easy. Most of the mains were accessible from the unfinished basement. Except this one. The base of this main was only accessible through a small floor hatch in the lobby. Then, you had to crawl about 20 feet down a 2 feet by 2 feet tunnel. Luckily, there was a union at the base of the 2-1/2-inch main. Two of my smaller techs managed to crawl back to the main, break loose the union, and clear out almost 100 years of rust, scale, sediment and corrosion that had clogged the pipe. They used a combination of threaded rod, fish tape, and a water hose to flush out all of the debris. When they finally broke through the clog, the entire seven-story column of water burst out like Niagara Falls, soaking both of my techs from head to toe.
With the main and return pipe flushed out and clear, the steam flowed freely and condensate drained quickly. All the radiators on this tier now heated properly and the water hammer disappeared. Steam is a different animal. You can’t see what is going on inside the pipes. You must have the imagination to envision what is going on to understand a correct the problem. And, remember to watch that water line.
Dan Foley is president and owner of Foley Mechanical, Inc. based in Lorton, Virginia. (www.foleymechanical.com). FMI specializes in radiant, hydronic and steam systems as well as mechanical systems for large custom homes.
Leave a comment
Related Posts
We always have turkey for Thanksgiving. I mean who doesn’t? My job wasn’t to cook it, though; it was to eat it.
I had written a story for Plumbing & Mechanical a while back about a fella in Canada who sent me this email: "Our problem is that five out of hundreds of univentilator co...