This all-technical, three-hour seminar will make you familiar with the many types of old steam heating systems and what goes wrong with them. Dan Holohan’s easy-to-follow...
How Vacuum Can Form in a Steam System
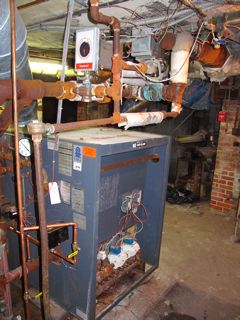
I heard from an old friend the other day. This guy works in Brooklyn, NY, and usually on some very interesting stuff. He's not one to say fuggedaboutit when there's a problem on a job. Here's what he wrote.
"Dan, I just finished installing a new Weil-McLain LGB-4 gas-fired boiler. This boiler is providing steam for a steam kettle in a commercial kitchen in a school. We installed main vents, a bucket trap for the main return line, and a Float & Thermostatic trap for the kettle. We also installed a condensate-receiving tank since we don't have enough height for the condensate to return to the boiler by gravity alone. We have a solenoid valve on the tank for feed water, as well as a tank overflow line to a drain, and a vent line so that the air can leave the kettle and vent from the tank.
"Today was the first time that we fired the boiler, and it went just as we had planned. After we cycled the boiler a few times, though, we shut down the system and watched as something very interesting happened. After the boiler started to cool down, water started to enter into the boiler, even though the feeder on the boiler was satisfied and the water was at the proper level. It just kept rising. And by the way, we have a spring-loaded check valve between the condensate pump and the boiler. I am sending you some pictures of the job."
I was in my car in the parking lot of an open-air shopping mall when I got his e-mail. It was pouring rain and I was waiting for The Lovely Marianne to finish shopping, which is sort of like doing time in a Super Max penitentiary.
My buddy had sent a lot of photos attached to his e-mail, and my phone was taking its sweet time downloading them because of me being in the penitentiary and all, so I just called him. Sometimes it's quicker to be old-fashioned, and besides, I didn't need the photos to know what was wrong with this one.
He told me how he and his helper watched the water fly up the boiler's gauge glass. "It was like it was being sucked right in," he said.
"It was," I said.
"What do you mean?"
"The boiler was sucking it in," I said. "Well, actually, the atmosphere was pushing it in, but you get the picture. There was a vacuum inside the boiler. It happens a lot with this sort of installation."
We talked about it and I got him thinking like steam, which always makes this stuff easier to understand. You just have to pretend you're the steam and then think about what you would do inside that system.
For instance, you begin as water in the boiler. The fire comes on and you get hot. When the flame adds enough sensible and latent heat to you, you decide it's time to change state from a liquid to a gas, and at that point, you go off like microwave popcorn. In fact, you go off even better than popcorn. You expand 1,700 times, shoving all the air that's around you toward the steam kettle. The air passes through the kettle, enters the kettle's steam trap, sails right through that trap and leaves the system through the vent on the condensate receiver.
As steam, you're now in the kettle. You can't get out of the kettle because of that steam trap (steam traps trap steam). So you give up your latent heat to the soup in the big kettle, which causes it to boil, and then you start shrinking back into liquid water. And as you do this, it would be wonderful if the air could work its way back into the kettle to fill the empty space you're leaving behind as you condense, but that steam trap is still closed. So what gets left behind in the kettle, and in the boiler (all the way back to the boiler waterline) is a vacuum.
With me so far? Good. Now think of the waterline in the boiler. It has a pressure above it that's lower than the pressure of the atmosphere. The water in the condensate receiver, which vents to the atmosphere, has atmospheric pressure sitting on top of it. In Brooklyn, this happens to be 14.7 pounds per square inch.
Okay, we have two containers of water (the boiler and the condensate receiver), and they're connected with a pipe. One container is under a pressure that's higher than the pressure that sits atop the other container. Separating these two containers of water is that pipe, and in that pipe there's a spring-loaded check valve. This is facing in the direction of the container that contains the low pressure.
Have you ever put air in your car's tires? High pressure goes to low pressure, right? You bet it does. Always. So the water inside the condensate receiver is going to flow into the boiler and flood it. From the outside, it looks like something is wrong with the automatic water feeder, but that device is innocent, so don't curse it and don't replace it; it's not at fault.
"You need to add a vacuum breaker to the boiler," I told my friend. "Put it anywhere above the boiler waterline and you'll be fine."
"Simple as that?" he said.
"Yep, and then you can fuggedaboutit," I said.
Simple, right? Here's the other place where this can happen, and this is a bit more complicated.
Nowadays, when you replace a steam boiler that serves a big building you'll often find a vacuum pump on the return piping. Engineers specified those pumps because those pumps increased the differential pressure between the steam-supply pipes and the condensate-return pipes. That allowed the engineer to downsize every pipe, valve, and fitting in the building, which cut costs on the installation, but which also means that once it's a vacuum system, it's always a vacuum system.
When you change the boiler, you're probably going to be installing a replacement that doesn't contain nearly as much water as the old boiler held. That's just the nature of modern steam boilers. The new boiler may need a boiler-feed pump to hold the water that used to be in the old boiler, but isn't in the new one. The challenge is that the system still needs the vacuum pump because of the size of the pipes throughout the building.
So here's what you'll do. You'll install the new boiler-feed pump between the new boiler and the old vacuum pump. The vacuum pump will start with the burner and pull the air from the system. It will suck the air from the return lines, the radiators, the supply mains, and all the way back to the boiler's water line. The steam will follow, and when the condensate returns to the vacuum pump, the vacuum pump will discharge it into the new boiler-feed pump.
And that's the problem. You see the new boiler-feed pump has a vent that's open to the atmosphere. It's not part of the vacuum loop that makes up the rest of the system (boiler, to supply mains, to radiators, to return mains). As the vacuum pump sucks on the system, it's also sucking on the air from the surface of the boiler water. At that point, the atmospheric pressure inside the vented boiler-feed pump's receiver will shove the water that's in the receiver into the boiler and flood it.
You can't use a vacuum breaker this time because you have a vacuum maker on the return. Having a vacuum maker and a vacuum breaker in the same system is like having a humidifier and a dehumidifier in the same room. They'll just go to war with each other to see who's the toughest.
Here's how to solve this problem. Instead of using a spring-loaded check valve between the boiler-feed pump and the boiler, use a motorized valve. Control the motorized valve with a pump controller on the boiler. When the boiler needs water, it will open the valve, which, in turn, will start the boiler-feed pump though its end switch. The boiler will get the water it needs, and once the motorized valve closes, the atmosphere won't be able to shove any unwanted water into the boiler.
And then you, too, can fuggedaboutit.
One last thing. On every steam system that has a vacuum pump, you'll also see a small equalizing line that runs from the pump's receiver to the boiler. This line will dip down at some point to form a U-tube that will always have water in it. In the low point of that U-tube there will be a check valve that points toward the boiler.
This line is there to equalize the natural vacuum that can form inside the supply mains and radiators during the fall and the spring when the pipes are cold on start-up. That naturally induced vacuum, caused by that 1,700:1 ratio of contraction when steam condenses, can cause a greater vacuum in the supply lines than the vacuum pump is making in the return lines, and that will keep the condensate from leaving the radiators. Equalizers equalizer.
None of this is that complicated. Just think like steam.
Leave a comment
Related Posts
We always have turkey for Thanksgiving. I mean who doesn’t? My job wasn’t to cook it, though; it was to eat it.
I had written a story for Plumbing & Mechanical a while back about a fella in Canada who sent me this email: "Our problem is that five out of hundreds of univentilator co...