This all-technical, three-hour seminar will make you familiar with the many types of old steam heating systems and what goes wrong with them. Dan Holohan’s easy-to-follow...
Modular Steam Boilers
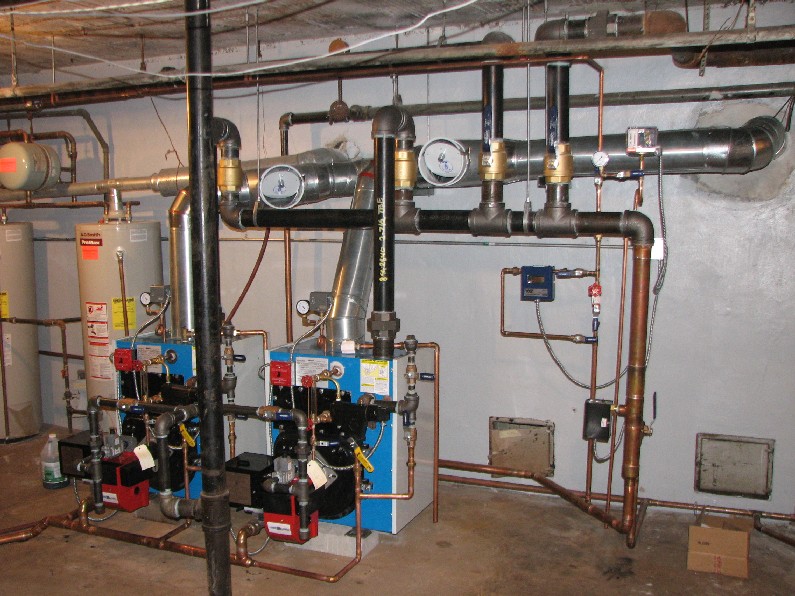
Modular steam boiler systems can look very attractive when it comes time to replace an old steam-heating boiler. The people who sell these systems promise ease of installation and energy savings. But how you pipe those boilers - both individually and then together - will either make or break the job.
Here are a few points to keep in mind if you’re thinking modular:
First, steam is dynamic. It can move at 60 miles per hour in a steam heating system and still be within the normal design range. As it moves, steam loses pressure though friction and condensation. How much pressure it loses depends on the pipe size and configuration, whether or not you’ve insulated the pipes, and the boiler’s Gross load. Because steam is dynamic (always moving, and always dropping in pressure), the pressure at any two points in the system will never be the same. This is true even after the system has heated from one end to the other.
I mention this because it’s easy to confuse steam with compressed air. You might think that once you get some pressure at the boiler, that same pressure will be everywhere in the system, as it would with compressed air. But that’s not the way steam works. Steam can condense; it’s always losing pressure.
As it whips its way through the common header, the steam can affect the water lines in the individual boilers. A mere one-ounce difference in steam pressure equals a 1-3/4-inch difference in water column, and depending on how you pipe the system, this can present you with a real challenge when you’re trying to balance your boiler water lines. And that’s why you should never interconnect modular boilers on their condensate-return side.
Here, forget modular systems for a minute and imagine you just specified two big boilers to provide heat for an old elementary school. One boiler is a stand-by to the other. You plan to have the superintendent alternate the boilers once each week during the heating season.
Now, if you look in any steam-heating text, you’ll see that when you have two big boilers such as these you have to pipe each one with an independent condensate-return line. If you connect both of those big boilers to a single boiler feed pump through a common condensate-return manifold, the water from the feed pump won’t know where to go. It can’t possibly enter both boilers equally because the boiler that’s firing will be under a slightly greater pressure than the boiler that’s not firing. The water lines between those two supposedly "equalized" boilers will never be the same. The feed water will enter the boiler that’s off at a greater rate then it enters the boiler that’s on. The "on" boiler will then shut off on low water, and at that point, the steam pressure will drop, and the boilers will equalize. The "on" boiler will restart, and then stop again as it loses more water to the "off" boiler. Short-cycling such as this kills your combustion efficiency.
But worse than that, after a number of feed cycles, both boilers will probably flood. And as the water level gets closer to the exit nozzle, the steam will carry boiler water into the header and possibly into the system piping. That leads to wet steam, unbalanced distribution, water hammer, and high fuel bills.
Check any good steam-heating text, and you’ll see that to make the two big boilers work together you have to either provide each boiler with either an independent feed pump or a motorized valve. Each pump or motorized valve takes its orders from the individual boilers’ pump controllers. Piped this way, feed water can flow only into the boiler that needs it, and never into a boiler that’s off.
Now change things around a bit. Instead of using two big boilers let’s use, say, five little boilers. We’ll connect them all together on the condensate-return side, and we’ll feed them with a single boiler feed pump that takes its direction from a single pump controller. We’ll mount that controller somewhere in the middle of the group of boilers.
What do you think? What’s going to happen when the feed pump comes on? Will the laws of physics change just because we’re using small boilers instead of big boilers? Will the water suddenly gain the intelligence required to flow only into the boilers that need it? Or will the water simply enter the "off" boilers because that’s where the pressure is lowest?
I think you’re making a big mistake if you interconnect those returns on your modular systems. Each boiler should have a pump controller and a motorized valve with an end switch that will start and stop the feed pump. Without those segregated condensate-return lines your individual boiler water lines will be bouncing like the cylinders in a V-8 engine.
Now, here’s something else to consider, and this is on the supply side, not the return. The water inside an "on" boiler will naturally be hotter than the water inside an "off" boiler. No surprise there, right? So you shouldn’t be surprised when the steam from your "on" boilers travels through the common header and condenses inside your "off" boilers. Where there is relatively cold water, steam will condense. There’s no getting around that.
This is a common cause of boiler flooding in any steam system that has more than one boiler. It’s the reason why when you open those steam-heating textbooks you’ll see either a gate valve or a check valve on the main supply leaving each boiler. If you don’t find these valves on the job (because they can be real big and very expensive!), you’ll probably find a "spill trap" in the header equalizer. This trap (usually a 3/4-inch F&T) sits at a point in the equalizer that’s slightly higher than the operating level. As steam condenses in the "off" boiler, the excess boiler water will open the trap and spill back to the boiler-feed pump. The ASME Boiler Code shows this as an acceptable solution to this common problem.
You would be wise to specify a spill trap in the equalizer of each modular boiler, or a check valve in the steam supply line of each boiler. And it wouldn’t hurt to specify both because boiler-water level is critical when you consider the limited amount of steam-disengaging space inside a small, modern steam boiler. A rising water level can cause boiler water to carry-over with the steam. It winds up in the header, and leads to wet steam.
The installation diagrams some modular steam boiler manufacturers publish also show low-water cutoffs on some, but not all, of the boilers. I think every steam boiler needs a low-water cutoff. If you provide motorized valves on your return piping, your pump controllers on the modular boilers will perform the low-water cutoff function.
Individual near-boiler piping is equally important but often overlooked in modular systems. If you installed just one of the small boilers you find in a modular system, you’d have to pipe it with a proper header, an equalizer, and, if it were a gravity return system, a Hartford Loop (you won’t need Hartford Loops with your pumped return lines). If you didn’t pipe the boiler this way, you would be violating the boiler manufacturer’s piping instructions.
Boiler manufacturers make a big deal out of these instructions (as they should!). Nowadays, you have to consider the near-boiler piping to be a part of the boiler because it acts as a steam separator. The exit velocities of modern steam boilers are far too high to produce dry steam without help from the near-boiler piping.
The near-boiler piping rules that apply to an individual boiler should also apply when you pipe that little boiler into a modular system. You’ll be making a mistake if you connect the steam supply directly out of the boiler into a common header without benefit of individual headers and equalizers.
You’ll get the best results from a modular steam boiler system if you pipe each boiler as though it were standing alone (with a proper header and equalizer), and then feed off each individual boiler header into a common drop-header. The term "drop-header" comes from the way the individual boiler supplies approach this header. The supply tapping from each boiler header rises to a point higher than the drop-header, and then takes a two-elbow turn to connect into the top of the drop-header. If you size the drop header to handle the entire load of the system at the proper velocity your modular boiler system will deliver the driest steam possible to the building.
Supply steam to the building through one or more mains, which you’ll take from the top of the drop-header at a point between the last supply from the modular boilers and the end of the drop-header. To keep any carry-over water from bouncing up into the mains, connect them not closer than 12 inches from the end of the drop-header. Drip the end of the drop header through an F&T trap back to the boiler-feed pump. This F&T trap is usually very small because if you size and pipe everything properly, it won’t have to handle much carry-over or condensate.
Not every steam boiler manufacturer goes to the trouble of incorporating these design elements into their modular systems. I suppose they’re concerned about first costs, but I would never recommend a modular steam boiler system without insisting that it be piped this way.
Leave a comment
Related Posts
We always have turkey for Thanksgiving. I mean who doesn’t? My job wasn’t to cook it, though; it was to eat it.
I had written a story for Plumbing & Mechanical a while back about a fella in Canada who sent me this email: "Our problem is that five out of hundreds of univentilator co...