This all-technical, three-hour seminar will make you familiar with the many types of old steam heating systems and what goes wrong with them. Dan Holohan’s easy-to-follow...
Steam Boilers for Breweries
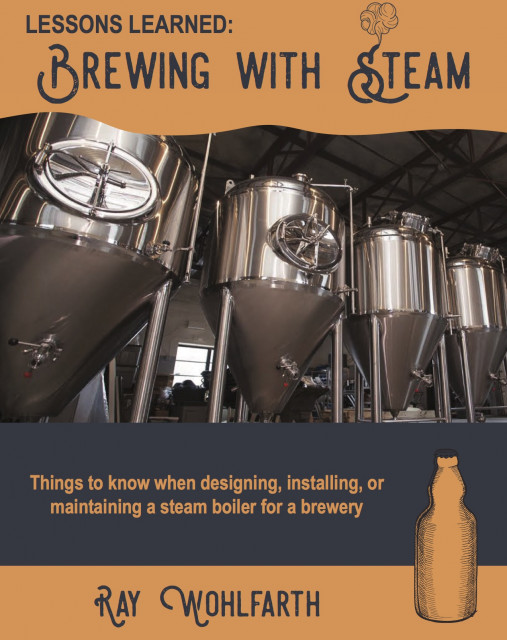
Here are some excerpts from my new book, Lessons Learned: Brewing with Steam. I wrote it to help you design, install, and maintain steam systems used in the craft brewing and distilling business.
Craft breweries are opening at a rate of one new one per day and most require a steam boiler in their brewing process. Craft distillers are projected to have the same growth curve. Brewery and distillery steam systems are much different than space heating applications as comfort steam heating systems are designed to operate on 2 pounds of pressure while many brewers and distillers operate at pressures almost 7 times higher.
I attended a seminar and met a beer industry expert who instructed the attendees to operate their steam boilers between 12 and 14 ½ psig. After the seminar, I met with the man privately and respectfully disagreed with him about his operating suggestion. I explained how low pressure steam systems are not meant to operate at that pressure and told him a boiler operating that high could lead to many production issues. The real magic with steam is the latent heat surrendered when the steam turns back to condensate. In reality, there is only a 4 Btu difference between 11 and 14 Psig.
Understanding how steam works
If you are installing a low-pressure steam boiler for a brewery or distiller, throw out everything you know about hydronic boilers. The operation of a steam system is closer to the operation of an air conditioning unit than it is to a hydronic boiler. The water inside a boiler will change state from a liquid to a vapor and then back to a liquid during the heating process.
Dry Steam
Try to imagine you are hiking in the woods on a bright sunny day, feeling good about being outside in nature. You see a storm cloud and suddenly the clouds open and rain is everywhere, turning the path you are on into a muddy mess. Each step becomes more difficult as the mud sticks to your shoes, slowing your progress. This is similar to what happens when the water from the boiler becomes entrained in the steam. This is called carryover and it makes the system to work harder. The extra effort of the steam causes it to condense prematurely sucking the energy from the steam. Steam systems are designed to heat using dry or pure steam. The term Dry Steam is confusing itself, as steam is nothing more than water heated high enough to change state and become a vapor. To operate the system properly, try to limit the amount of water in the steam, as the water will cool the steam, reducing the efficiency and effectiveness of the system.
Steam is basically lazy and not very smart. All steam wants to do is surrender its latent heat and revert back to water (its natural stat). Let us assume we have a quality steam boiler that produces dry steam in the range of about 95-99% pure, which means we have 1-5% water in the steam. The system uses the steam pressure to push the steam through the piping looking for someplace cool to surrender its heat at a speed of about 40 miles per hour. The friction inside the piping and the heat lost through the piping into the building causes some of the steam to condense, which lowers the steam volume. Since the condensate is cooler than the steam, the steam thinks it has found the place where it is supposed to give up the latent heat and begins to condense. This causes a ripple effect and pretty soon, the volume and temperature of the steam is much lower, reducing its ability to heat your process.
Boiler Safety Valve
A safety valve is installed on every boiler to prevent over pressurization inside the boiler. It is designed to open when the internal steam pressure is above the setpoint of the valve. Low-pressure steam boilers have a safety valve setting of 15 PSIG. Many safety valve manufacturers do not want the boiler operated at the setting of their safety valve, as it could cycle open and closed, ruining the safety valve. For example, the installation instructions for a Conbraco Model 12-14 safety valve states, The minimum required pressure margin for this type of valve is 4 PSI. UNDER NO CIRCUMSTANCES SHOULD THIS MARGIN BE LESS THAN 4 PSI! This means the boiler pressure setting should be no higher than 11 psi on a low-pressure steam boiler. If the boiler is operated close to the setting of the safety valve, it may open and push all the steam and water from the boiler. The discharge of the safety valve should include a drip panel, which will limit the weight on the relief valve and allow the drainage of any water in the discharge pipe of the relief valve. The outlet of the relief valve should be piped outside to avoid opening inside the building. Steam quickly fills the room making visibility almost non-existent. It also displaces oxygen so breathing is difficult. The steam could also find its way into electrical components creating a dangerous situation. Lastly, the steam could burn anyone it comes in contact with. A 3rd degree burn could occur within one second when exposed to steam.
Good luck when designing, installing, or servicing the steam boiler for a brewery or distiller and remember: they are not like a space heating system.
Want to learn more? Check out Lessons Learned: Brewing with Steam.
Leave a comment
Related Posts
We always have turkey for Thanksgiving. I mean who doesn’t? My job wasn’t to cook it, though; it was to eat it.
I had written a story for Plumbing & Mechanical a while back about a fella in Canada who sent me this email: "Our problem is that five out of hundreds of univentilator co...