This all-technical, three-hour seminar will make you familiar with the many types of old steam heating systems and what goes wrong with them. Dan Holohan’s easy-to-follow...
Taking Another Look at Steam Boiler Sizing Methods
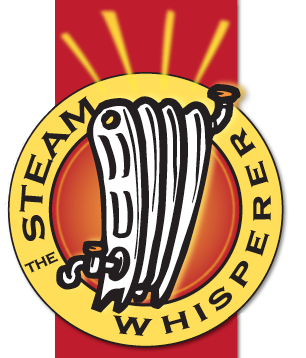
Due to the efforts of many sharp minds in the steam heating industry and simple economics, standing cast iron steam space heating systems are no longer wastefully being thrown away like last years favorite toys. There is a growing number of contractors and engineers that know how to make these systems run well and are applying that knowledge to bring many crippled systems into good working order, giving owners a great opportunity to “green up” their buildings or homes. These systems are now providing silent, comfortable heating with low fuel usage when compared to other modern alternatives, largely due to the more efficient radiant heat they provide and reduced distribution system losses.
However, there are some fundamental issues that currently limit the efficiency potential of many steam heating systems, especially those with standing radiation (cast iron radiators). The first and often most talked about, is that steam heating systems run at such high temperatures, they cannot take advantage of condensing technology like hot water or forced air systems. This amounts to a maximum of 7% to 10% loss of conversion efficiency. This limitation has already been overcome with large commercial boilers such as the “Super Boiler” project now in advanced testing in real life applications. Hopefully, the technologies employed will gradually make it down into the smaller boilers that are typically employed for space heating.
The other main limitation, and a much larger one in this authors opinion, is related to the fact that many (if not most) of these systems have excessive radiation when compared to the current heat loads of the structures they serve. These are the typical one or two pipe systems installed decades ago, especially those installed around 1900 when systems where sized to heat a structure with the windows open at night in sleeping rooms. In addition, over the years, the heat loss of these structures probably has been reduced due to improved windows and added insulation, causing the systems to be even more oversized. These systems are everywhere and provide a huge opportunity to go “green with steam” if they can be made to run at optimum efficiency.
Current industry accepted practice for sizing steam boilers for these systems is to size the boilers to the heat output of the standing radiation plus the heat loss of the piping system (usually another 15% or so) plus an additional pick up factor (about another 15%) to help bring the system up to operating temperature quickly when heating is needed. In the hands of skilled installer and with properly functioning system equipment, this typically results in a system that heats evenly and at dramatically lower fuel usage than the many grossly oversized existing steam boilers.
This is all well and good, unless you happen to also run a current day heat loss of the structure. If you do this, it is likely that the boiler will be at least 50% oversized and, in most systems, 100 to 300% oversized when compared to heat load. This makes me pause and think that we may be leaving an awful lot on the table in terms of efficiency of our steam systems. It also greatly increases the cost of the replacing the boiler.
Most of the boilers that are installed in steam systems are on/off boilers. In addition, when using natural gas, most are also open atmospheric designs that have enormous stand by losses, especially when they are operated at low loads. Stack dampers help, but the waste heat is dumped into the boiler room so there is still waste, just not as much. Using a power burner boiler design addresses a lot of this waste, but short firing cycles due to the equipment being oversized still takes its toll on efficiency.
However, if we go back to the system itself and begin again to look at what makes these systems work, some new alternatives emerge for both one pipe and two pipe systems.
We’ll look at the one pipe steam systems first.
One of the keys to making these systems work better is to look at how they originally operated. These systems were designed with coal fired boilers in mind. When these great big old boilers were fired, the fire built slowly, and due to the large mass of metal and water, steam production was also very slow to build. The system filled with steam very slowly since there was very little steam being produced until the fire grew and the boiler got up to full temperature.
Now compare this to our current boilers sized with current methods. The chief goal is to get the system piping heated up very quickly and the radiators completely filled with steam ASAP. This is a complete opposite to how these systems originally worked.
Even with this goal in mind and a generously sized boiler, the radiators rarely if ever heat all the way across because the thermostat is satisfied long before the system is completely filled with steam. This then begs the question….. Why are we sizing steam boilers to completely fill the system with steam? And another follows….Why do we need to get the system up to temperature so quickly, when the system originally did not work that way?
I suspect it may have a lot to do with the classic American mentality that faster (and bigger) is better. The capacity of the radiator vents now used on systems is much greater than were used in the coal era. Just a quick look at the venting capacity charts developed a few years ago by Gerry Gill and Steve Pajek will show this pattern. The classic Hoffman #1 was rated at .016 CFM at 1 ounce of pressure, with the old No.40 registering .042. Now take a look at the vents often used today…..the Gorton #6 at .150, the Gorton D at .330, the Heattimer varivalve at 50% setting at .340 and full open at .516. If you do the math the venting of these newer vents is up to 32 times faster than the old. Just think, one radiator today can have the same amount of venting capacity as 32 radiators in the old days. This has a huge impact on how the system heats and I’ll show you why.
Let’s take a typical smaller system tuned by a top notch steam expert. The boiler is sized generously, often with an extra large pick up factor to account for the extra piping that still exists despite many radiators being removed. The mains have nice big main vents, let’s say 3 Gorton #2’s total, and with venting rates of 1.1 cfm per vent (a total of 3.3 cfm). This allows air to vent quickly so steam can get to the end of the mains quickly. The 15 radiators are also generously vented so the steam can enter them quickly and easily, each with a vent averaging about .340 (the middle setting of a Heat Timer varivalve) which gives us a total radiator venting of 5.1 CFM.
Did you notice something already? We have more venting capacity on the radiators than the mains. We better make a lot of steam in a hurry if we want to drive the steam down the main before it starts filling the radiators. If we don’t, the steam, being lazy, is going to take the easiest path……right towards the first few radiators. This leaves the rest of the radiators cold, causing the typical problem when an “undersized” boiler is installed. We need that bigger boiler to make sure all the radiators heat, in other words to keep the system in balance.
Now, what if we go back to the older radiator air vent capacities and see what happens? We still want to vent those mains well to let the air can get out quickly, so we’ll still use 3 Gorton #2s (3.3 cfm) However, lets say we use an average venting rate of .042 on the radiators (the capacity of the old Hofmann #40) for a total venting rate of 0.63 cfm for the radiators. See what’s happened? The main vents now have over 5 times the venting rate of the radiators, so you can guess where the steam will go first…..to the end of the mains. If we use the venting rate of the old Hoffman #1 the steam will favor the mains even more. The radiators would vent only at 0.24 cfm and the mains at 3.3 cfm. The mains would have nearly 14 times the venting of the radiators.
Many will say there is no way you can vent radiators that slowly, the vents will howl and not last very long. The problem with this thought is that is how they used to be vented. What you now need is more time for those radiators to vent, and the way to give them more time is to reduce the steaming capacity of the boiler. The smaller vents will hold back the steam from the radiators while the big main vents allow the steam to fill the mains all the way to the end. Once the mains are filled, the system pressure will increase, since the piping is no longer condensing steam and the radiator vents will begin to vent more rapidly, allowing steam to enter the radiators. Once steam enters the radiators, the venting capacity can remain lower, since the radiators condense steam a lot more quickly than an insulated steam pipe, so less air needs to be vented to make room for the steam.
You may well see this as a potential solution for systems that are not heating evenly due to “undersized” steam boilers….cut down the venting rate of the radiators and vent the mains well. Well you’re right and in doing so we will be following the advice of one the ancient guru’s of steam “Vent your mains quickly and your radiators SLOWLY, but completely”.
If you stop and think about this for a moment, this technique also provides the foundation for a new approach to sizing boilers. If we can get a system to heat evenly with an “undersized” boiler, why would we want to put in a bigger boiler? Maybe it needs to be bigger to meet the heat loss of the house on the coldest day, but why put in a boiler bigger than necessary. Anything bigger will invite shorter firing cycles, especially in warm weather, which greatly hurts efficiency and increases wear and tear on the boiler and system (ie thermal cycling and production of acidic condensate. Also, nice long firing cycles at lower input should provide much more stable interior temperature, so heat losses at or near the ceilings will be lower since that huge cloud of hot air will diminish greatly (think outdoor reset on a hot water system)..
So just how much smaller can you go? Well the first obvious limitation is that you need to produce enough heat to heat the building on the design day (just like hot water boilers).
The next may be related to the balloon concept of steam heating. The boiler needs to be able to be constantly filling the system with steam (blowing up the balloon) in order for the system to remain balanced when using radiator vent sizing to balance the system. This goes back to the way we can tame oversized radiators by limiting the air venting. So long as all the radiators are being filled with steam, the air vent capacity determines the amount of heat the radiator, or the room, gets. However, if we fill all the radiators completely, the rooms with oversized radiators will now overheat. If the system is oversized compared to the actual heat loss (most one pipe systems are), this is only likely to happen during recovery from setback. Many steam system owners have discovered this phenomenon….buildings heat evenly if stable temperatures are maintained, but everything goes out of balance if setbacks are used. Remember, it is rare or never that radiators heat all the way across on our steam systems, since the thermostat is satisfied well before the radiators fill completely with steam.
One final limitation is simply the fact that the lower the steaming capacity, the smaller the radiator vents need to be to maintain balanced heating. The smallest vent we can use sets the bottom limit on the boiler capacity. We also probably want all the vents to be infinitely adjustable to permit fine tuning of the system once running. The Hoffman 1A and Ventrite #1 appear to get real close to that old Hofmann #1 venting capacity. I use the 1A’s since I am in Chicago, Hoffman’s home.
The limits on this technique are still not clear, but I encourage you to take the first step. A good starting point is probably using a boiler that can be fired to the conventional full radiation + piping and pick up load and then using an adjustable input burner. For natural gas I have been using the Slant Fin Intrepid series with either a HeatWise gas burner or PowerFlame X4M burner if I want modulated input. With oil burners the choices are much broader (I do almost no oil work in my area). Start out by removing the pick up factor from the burner input and set up the burner for that load. Then get your mains vented really well. Clean up your boots and take a walk upstairs with an armful of adjustable vents that can go really low and set the vent on the smallest radiator for the lowest setting and provide a little more capacity as the radiators get larger and need more venting. I’ve found that you usually don’t want to go over about 2 ½ on the Hoffman 1A’s initially.
Fire that boiler up and be very, very patient. This is the scary part because the system will heat up very slowly…..maybe 20 or more minutes until the radiators start getting heat. This is especially the case when the boiler is not clean yet and you’re making wet steam. Just remember, this is how the system originally started up with coal. You may need to open some vents up to 3 or 4 if you have some radiators that don’t provide enough heat to the rooms.
If you get comfortable with this, take the next step to down fire the boiler so you get closer to the actual heat loss of the spaces (don’t forget the piping loss will always be there unless these spaces are also heated). I suspect that the farthest you can take this is using the total of the heat loss + piping loss + about 15% to make sure on the coldest day the boiler can still be blowing up the system when the thermostat is satisfied.
Get that boiler good and clean and you may be in for a pleasant surprise, you’ll end up with a steam boiler running very long, steady and efficient firing cycles, with short off times that greatly cut standby losses and provide incredibly stable heating to the home. The homeowners will see nice low fuel bills because you now have made the boiler operate even more efficiently than it is rated, rather than the other way around because the system, and therefore the boiler, is oversized for the actual heat loss.
(Copyright, Dave Brunell, 2009. To learn more about Dave, click HERE.)
Leave a comment
Related Posts
We always have turkey for Thanksgiving. I mean who doesn’t? My job wasn’t to cook it, though; it was to eat it.
I had written a story for Plumbing & Mechanical a while back about a fella in Canada who sent me this email: "Our problem is that five out of hundreds of univentilator co...