This all-technical, three-hour seminar will make you familiar with the many types of old steam heating systems and what goes wrong with them. Dan Holohan’s easy-to-follow...
The Importance of pH in Steam-Boiler Water
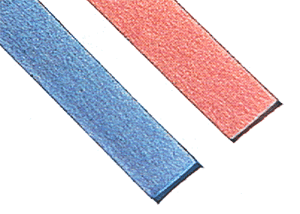
What’s the cheapest tool you can carry if your business includes taming old steam-heating systems and making them purr with greater efficiency?
Litmus paper!
You probably learned about the power of hydrogen in grade school. Your science teacher introduced you to litmus paper and let you test lemon juice and baking soda and whatnot. It was an easy lesson. The juice was acidic and the baking soda was alkaline so the juice showed a low pH by turning the litmus paper a certain color; and the Arm & Hammer showed a higher pH by doing a similar thing. The pH scale went from zero to 14 and the number seven was neutral.
When we measure pH, we’re measuring the power of Hydrogen. The number refers to the relative concentration of hydrogen (acid) and hydroxide (base) ions in solution. Gosh, I’m such a scientist.
It comes into play with steam boilers because a pH between 7 and 9 (slightly alkaline) is just right. If the pH is lower than that, the water will start eating the pipes. If it’s higher than that, the water won’t corrode metal, but it may begin to foam, and that’s not good.
Hold that thought for a moment.
You’re on a job and you have a steam boiler that’s taking on a lot of feed water because the system has leaks. You know you should fix the leaks, but your customer is a cheapskate and he believes in the laws of economics more than he believes in the laws of physics He likes band aids. He thinks it’s cheaper to keep adding feed water to the system (even if it’s not), so that’s what’s been going on for a while. And there you are.
Here’s the real problem: Fresh feed water brings with it carbonates and bicarbonates, which are both natural and normal. The challenge starts when the water boils because carbonates and bicarbonates break down and leave the boiler as carbon dioxide. This gas flows through the system with the steam, and if you’re not venting the system well, the condensate will absorb the carbon dioxide as the steam gives up its latent heat to the pipes and the radiators. We call that Henry’s Law.
The system winds up with carbonic acid in the returns and that’s bad news because carbonic acid removes the thin film of rust that naturally forms on the insides of steel pipes. That mild rusting is a good thing to have because it helps protect the underlying metal from further corrosion. By stripping away the surface rust, the acid makes more fresh metal available for munching. Before long, you have leaks.
This is why it’s good to insulate the return lines in any steam system. The cooler the water gets, the more it will absorb gases such as carbon dioxide (Henry’s Law). Keep the condensate as hot as possible; it will be less acidic and the return lines will last longer. Your client will also use less fuel.
And even if you fix the leaks in the system, you still have to keep an eye on the pH of the water because many people add chemicals to their boilers to avoid corrosion. These chemicals shove the pH toward the alkaline side of the scale. When the pH reaches 10, corrosion becomes impossible. That’s what makes chemical drain cleaners safe for pipes. That nasty stuff has a very high pH (think lye).
The trouble really starts when someone gets overenthusiastic with the chemicals and the pH reaches 11. At that point, the water will foam, and that leads to wet steam, which wastes fuel because it robs the steam of its latent heat. The steam stops before it can reach the radiators and your client has to run his burner longer to heat the building, and with lousy results.
The classic, off-the-shelf chemicals the Dead Men used to adjust pH were baking soda and vinegar. Vinegar is slightly acidic (low pH), and baking soda is slightly alkaline (high pH). They’re inexpensive and they work, but if you use vinegar (or any other chemical), beware of the odor it can send upstairs in a building heated with a one-pipe-steam system. The air leaving the radiator vents will be smelly, and that can lead to lots of complaints. They’re liable to call a lawyer instead of you.
So use that cheap tool. Keep some litmus paper in your toolbox and check the pH whenever you blow down a low-water cutoff. It’s a simple test and easy to do, and by getting the water’s pH just right, you can solve a lot of problems that are costing money.
And no, the Dead Men did not use baking soda or vinegar to clean the water or the inside of the steam system. Hey, would you use either to wash your hands? Vinegar and baking soda don’t clean; they just change the pH.
And please keep in mind that all steam systems are open to the atmosphere, so there’s always going to be some evaporation and a need for feed water. But steam boilers that do only space heating reuse nearly all of the water because the condensate returns to the boiler from the piping and radiators. You shouldn’t have to add too much water to these systems unless they’re leaking. And in spite of what the cheapskate clients think, it’s always less expensive to fix the leaks than it is to keep adding fresh water or chemicals.
Feed water is cold and contains lots of oxygen. People who maintain industrial boilers deal with that oxygen by passing the feed water through a deaerator, but you’ll rarely see a deaerator on a space-heating boiler.
Henry’s Law tells us that gases dissolve in liquids in direct proportion to pressure and temperature. So the colder the water, the more oxygen it will contain. That oxygen comes out of solution as the water boils, and it can eat holes in the boiler, right at the boiler’s waterline.
If you decide to feed with hot water instead of cold water, the minerals in the water will come out of solution on the automatic water-feeder’s seat, and that can cause a flood, especially if it’s a one-pipe-steam system.
Feed water also contains suspended solids. The more feed water you allow in, the more solids you’re going to get. The solids collect on the surface of the water as it boils. They surround the steam bubbles as they form, making them tougher. Tough bubbles resist breaking, and that also leads to foaming and wet steam. The finer the suspended particles are, the more they will collect in the bubbles, and the worse the foaming will be. You probably can’t see these solids but they’re there, and this is why you must keep the feed water to a minimum. Fix those leaks.
What’s normal for feed water? Well, it depends on that system’s history. Has anyone kept track of how much water has entered over the years? Is there a meter on the feed line and a logbook nearby? Are the pipes leaking now? Are they buried under the floor? Do they go through walls? Are they in places you can’t see? Are the main air vents in crawl spaces where they may be leaking steam, but go unnoticed?
“Normal” is what traditionally happens from day to day. Have there been sudden changes? How will you know unless someone keeps a record?
I think every steam boiler that has an automatic water feeder should also have a water meter. Some of today’s electronic automatic water feeders incorporate a water meter into their circuitry, and these are worth the money because they tell you when something changes. If the system suddenly starts taking on lots of water, you know there’s a leak, and it’s either in the pipes, or it’s inside the boiler. Fix the leaks.
And none of this is complicated. Hey, you learned it in grade school.
Leave a comment
Related Posts
We always have turkey for Thanksgiving. I mean who doesn’t? My job wasn’t to cook it, though; it was to eat it.
I had written a story for Plumbing & Mechanical a while back about a fella in Canada who sent me this email: "Our problem is that five out of hundreds of univentilator co...