Recently I was asked to speak at the Rensselaer Renewable Energy & Sustainable Living Fair in New York, which took place on October 20, 2018. I was introduced to Frank Na...
Geothermal Design and Jobsite Examples
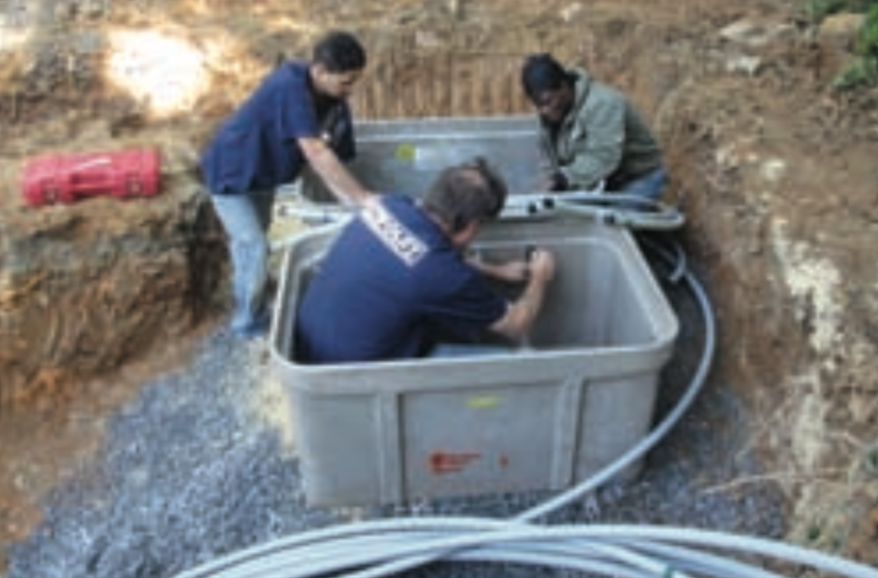
Since we work in a metropolitan area, the loop field can be a challenge at times. As we sub this part of the job out to a well driller, it can be more of a challenge, as it is not under my direct control. Luckily, we have two partner companies we use on a regular basis that make this less of an issue.
All of our projects to date have been vertical closed loop systems. I would not be averse to using a horizontal loop field but I have yet to land a project with the necessary space for this.
Two recent projects have tested the patience of my clients. The first was a large residential project in a close in D.C. suburb. Our client purchased several lots and is building a $20 million Taj Mahal in a neighborhood of $1– $3 million homes. The direct neighbors, already upset with the construction and associated nuisance, lost it when my sub started drilling 22 wells on a very tight lot. They were not prepared for the noise and vibration caused by over a month of drilling. The county inspector was out several times with noise complaints, water and silt issues and property damage complaints.
In retrospect, I would have approached the direct neighbors, introduced myself, apologized in advance for the nuisance and offered to repair damaged lawns or any other property damage. We are doing a smaller geo project just around the corner with nine wells and that is the tack the architect/owner took to minimize fallout from the neighbors. I’ve learned from this, and I will take a more proactive stance on future projects.
Some of the issues are just plain bad luck. We are doing a new house on a very tight infill lot in Cleveland Park, Washington, D.C. We require four vertical wells 360 feet deep; there is just enough space under the driveway for these four wells with no room to spare. Holes one, two and three went in without a hitch. When hole 4 got to about 220 feet, a fracture in the bedrock caused hole No. 2 to blow out. After cleaning out No. 2 and spending several days casing No. 4 and trying to re-bore with no success, we finally decided to relocate No. 4 about 15 feet to a spot that was inches from the lot variance. This bore went in with no problems. Some days you’re lucky, and some days you’re not.
I like to tie all my loops to a manifold located in a buried vault, as indicated in the photos below. This allows for isolation and purging of individual loops and for balancing, if required. I then run a pair of large dimension PEX mains back into the mechanical room.
We like to use heavy-duty concrete utility vaults to house the manifolds. They are more expensive than the plastic irrigation boxes, but I have found them to withstand jobsite abuse better than the plastic boxes. We use these same vaults for snowmelt manifolds, as well.
For systems with multiple geo systems, I will use a single pump with a variable-speed drive, similar to the one shown in photo on the right. This pump will vary its flow depending on the number of units online and can be controlled by delta-P or through the building BMS. On larger projects, we will also have a standby pump to minimize the chance of losing heating or cooling due to pump failure.
I once designed a large geo system that features a 40- bore geo loop field, seven water-to-water heat pumps piped and controlled to allow for simultaneous heating and cooling, twelve water-to-air units, one make-up air system and one water-cooled wine chiller split system. All of the pumps, including the geo loop pump, chilled water and hot water pumps feature variable speed drives (VFDs). Significant power savings can be achieved on these pumps by ramping down the pump speed during partial loads.
On all my geo projects, I use an expansion tank and air separator on the loop field. This same detail is also on the chilled water/hot water loop. The three-way motorized valves on the water-to-air units allow for simultaneous heating and cooling, which was a requirement for this 38,000 square-foot home. The water-to-air units also feature hot deck coils tied to the boiler for third-stage heat or backup heat in the event of a compressor failure. As this house also had radiant floor heat, we had triple redundancy on the heating side.
On this project, we used 2-inch, 3-inch and 4-inch L copper with Pro-Press fittings for the geo piping inside the structure. On our more recent projects, we have used Aquatherm polypropylene piping with fusion welded fittings.
Both systems have their pros and cons: Copper is a readily available product and Pro-Press is now stocked by multiple local vendors. We have used Pro-Press for about nine years; it affords tremendous labor savings. Aquatherm is relatively new to us. I had my entire field staff certified by the manufacturer and invested in the tooling. In addition to cost savings, we like the ease of assembly and the virtual leak-proof socket fusion welded joints. It is easy to keep the mechanical room neat, plumb and level with the straight lengths of pipe. Two local vendors carry this product, and it is gaining in acceptance.
I often see geo equipment mounted on plastic pads and even on a layer of rigid insulation. As the compressor is CONTINUED FROM PAGE 26 28 now inside, noise and vibration from the equipment are key considerations, especially when living space is directly adjacent to or above the mechanical room.
We prefer to pour a 3 1/2-inch concrete housekeeping pad and then to isolate the equipment using spring-loaded vibration dampening mounting hardware such as that manufactured by Mason Industries. These do a great job of dampening vibration and minimizing noise transmission. We will also use braided copper and stainless steel flexible connectors at the piping connection to minimize vibration transmission to the piping.
Balancing is a key consideration when installing multiple geo heat pumps on a single loop pump. Due to architecture and system layout, some units will be relatively close to the loop pump and some will be relatively far away. Pipe sizing will certainly help but this is not enough to ensure proper flow when multiple systems are calling simultaneously. Balance valves are essential. I prefer ten-turn, globe-style balance valves as they allow for precise balancing. I have also used combination control and balancing valves such as the Danfoss AB-QN.
I use an Alnor hydronic manometer to precisely measure flow and balance my systems. I tabulate my measurements in a spreadsheet for my TAB reports. My goal in mentioning products and manufacturers is to give specific examples and illustrate how we install our projects. It is not meant as an endorsement of one specific brand over another. In many cases, engineer specifications, local availability or long-standing business relationships dictate which product we use.
There are many different ways these geo systems can be installed; my way is certainly not the only way. If you have a different viewpoint, please share your thoughts with me. I enjoy the interaction and learn from my readers on a regular basis.
Dan Foley is president and owner of Foley Mechanical, Inc. based in Lorton, Virginia. (www.foleymechanical.com). FMI specializes in radiant, hydronic and steam systems as well as mechanical systems for large custom homes.
Leave a comment
Related Posts
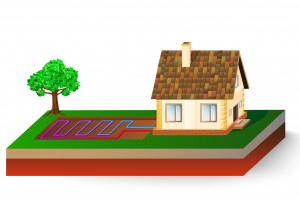
When I started my company ten years ago, I wanted to focus on radiant floor systems and mechanical systems for large custom homes. By and large, I have been successful in...
Pools are almost a necessity for many homes, and certainly for resorts and hotels. It’s not uncommon for pools in recreational centers to expend $50,000 per year for fuel...