Recently I was asked to speak at the Rensselaer Renewable Energy & Sustainable Living Fair in New York, which took place on October 20, 2018. I was introduced to Frank Na...
Getting Started with Geothermal
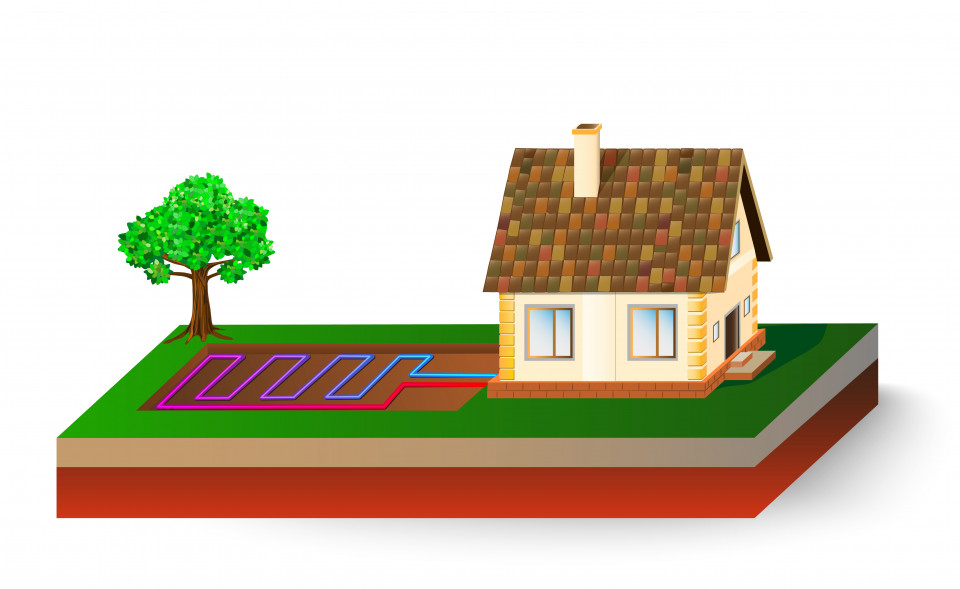
When I started my company ten years ago, I wanted to focus on radiant floor systems and mechanical systems for large custom homes. By and large, I have been successful in meeting that goal. About 40% of my business by dollar volume is in the custom home market, and the majority of my systems feature some form of radiant heat.
Early on, when I received queries on geothermal heating systems, also commonly called ground source heat pumps or GSHPs, I would pass the lead on to fellow contractors who were experienced in designing and installing these systems. As more and more of my clients began requesting geo systems, I had to rethink my business strategy. When 38 the federal tax credits went into effect, the requests grew dramatically, and I had to make a decision; educate myself on geo systems or get left behind.
About six years ago, I took the plunge. After attending manufacturer training and certification classes, my company did its first geothermal installation. We have since installed multiple projects, everything from small residential projects to an 80-ton, 19-system commercial project and everything in between. We currently have six geo projects in progress at various stages of completion. I have made many missteps along the way and have taken some lumps. I still have much to learn, but I will share my experiences with you.
As I sat in my first geothermal class, one thought struck me: While the equipment was new, and I had to learn some of the terminology, these were basically hydronic systems. The ground loop was the source, the heat exchanger was the load, and the physics of energy transfer through the piping and pump were the same as a hydronic heating or cooling system. In studying the piping diagrams, the lack of an air separator and expansion tank caught my eye. When I asked about this, I was told these were not needed in a geo system. Supposedly, the flexibility of the HDPE loop field piping and the small temperature deltas did not warrant the need for these devices. This made absolutely no sense to me.
I have installed air separators and dirt separators (or combi dirt/air separators) on all of our loop fields. I also install expansion tanks and pressurize the systems. I treat these as I would any other hydronic system. I have to say I don’t understand the concept of the “push/pull” pump stations with two pumps. I prefer to install one properly sized pump that pumps away from the expansion tank and point of no pressure change. Installed this way on a pressurized system, it minimizes the chance of pump cavitation.
As I have been called out to service systems not installed by my company, a common condition is a “flat” system where the loop field lost its pressure charge. Typically, the compressor is off on high head pressure due to a lack of flow in the loop field. In any system, there will be minute leaks through valve packing, flanges, threaded joints, etc. It does not take much for the system to lose its charge. This condition also wreaks havoc on the loop pump. A loss of charge can cause the inlet side of the pump to drop below atmospheric pressure, which can cause pump cavitation.
When I see a stack of 26-99s or 0011s in the corner, I know it is time to pipe in the expansion tank. A good quality air separator is essential to remove the dissolved air that will inevitably come out of solution. A pump cart won’t do this. A dirt separator will also help eliminate the sand and sediment that invariably finds its way into the loop piping as it is being assembled.
I am very conservative when designing my loop fields. I design around 85o EWT (entering water temperature) as I do not want to be short. It is not easy or inexpensive to correct an undersized loop field.
Last summer, I was called to look at an underperforming geo system. They had also recently lost two compressors in the system. When I surveyed the system in early June, before the heat of summer, the loop field was running at 109 F. Compressors don’t last very long running at 109 F condensing temperature. Capacity suffers dramatically as well. This loop field was drastically undersized.
During my survey, I found out that the owner had added an addition that included a wine cellar and commercial refrigeration equipment. All the new mechanical equipment was water cooled and tied into the existing loop field, which had already been designed to the edge of the envelope. I tried to explain that the loop field was like an ATM machine, you cannot withdraw more than what is in the account. This account was overdrawn!
Due to landscaping, hardscaping, stone walkways, stone patio, a pool, heli-pad and outbuildings, fixing this problem was nearly impossible without major demo and excavation work. An air cooled water tower was added temporarily to Band-Aid the system. I do not know how this was permanently resolved, as I politely excused myself from this one.
I realize drilling is expensive. In my market, we pay $15 – $18 a foot, depending on location and geology. It can be more on small infill lots in town. Additional casing, if required, can add to the cost. That is pocket change compared to going back and trying to fix a short well field. Be conservative in your design; it is cheap insurance.
Many of my projects have multiple systems. I have been on multi-system jobs where each system had its own pump station and loop field. Properly sized, there is nothing wrong with this approach, but, in my opinion, it is not an ideal design philosophy. The problem is that each loop field must be designed for peak load. Peak load rarely (or never) occurs in all zones at the same time, which leads to a wasteful design.
I prefer to design around one loop field that is sized for a diversified load. A typical system will have one variable speed loop pump that operates off an integral delta P control or a 0 – 10v signal from a BMS (building management system). Each heat pump will have a motorized valve at the condenser inlet. As systems come on line or cycle off, the variable speed loop pump will ramp up or down accordingly. I will install a standby pump that will automatically come online in the event of a primary pump failure. It will also automatically rotate for even wear. With this system, each heat pump “sees” the entire loop field, which helps manage peak loads easily.
Most of our early projects featured fusion-welded HDPE loop field piping. The last four or five projects we have done have featured the Rehau Rau-Geo system. I really like several features of this system.
- I like the heavy duty PEX pipe. It is tougher than HPDE and handles the jobsite abuse inevitable when pulling loops.
- I like the one continuous loop with no joints at the bottom of the well.
- I like the fact that all loops tie in to a manifold, which allows for flow measurement and balancing of each loop. It also allows for isolation of individual loops in the rare event that one is hit, allowing for at least partial system capacity.
- I like the four-pipe system (two loops per borehole), which increases the heat transfer capability.
Properly designed, installed and maintained, either system will work fine. I just wanted to share my experience with this relatively new product.
We typically run the loops back to a vault as shown in photo # ( ). We then run a large dimension PEX back into a basement mechanical room. This line is typically 2”, 2 1/2” or 3”, depending on flow requirement. This setup minimizes the wall penetrations required and keeps the mechanical room piping neat and tidy.
It is imperative to properly seal these wall penetrations. I have seen too many geo systems where the leaders were stuck through the foundation wall with some hydraulic cement slapped around the pipe. Invariably, the wall is stained by water leaks, and mud and sediment is puddled on the floor below the penetration.
I prefer to either core drill or sleeve the foundation and seal around the pipe with properly sized Link-Seal. This will ensure a watertight seal. If you do use sleeves, be sure to order the sleeves with the ring around the middle, which seals against leakage around the outside of the sleeve. I have seen jobs where the well intentioned installer used schedule 40 PVC for the sleeves and properly Link-Sealed the pipe. The problem occurred when the concrete shrunk away from the PVC and the leak path was around the sleeve. After backfilling, it is very difficult to fix these leaks. Spend a little time up front and save yourself from headaches and angry clients down the road.
Dan Foley is president and owner of Foley Mechanical, Inc. based in Lorton, Virginia. (www.foleymechanical.com). FMI specializes in radiant, hydronic and steam systems as well as mechanical systems for large custom homes.
Leave a comment
Related Posts
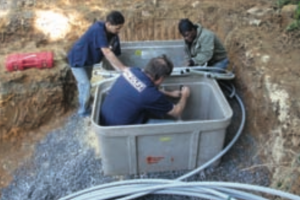
Since we work in a metropolitan area, the loop field can be a challenge at times. As we sub this part of the job out to a well driller, it can be more of a challenge, as ...
Pools are almost a necessity for many homes, and certainly for resorts and hotels. It’s not uncommon for pools in recreational centers to expend $50,000 per year for fuel...